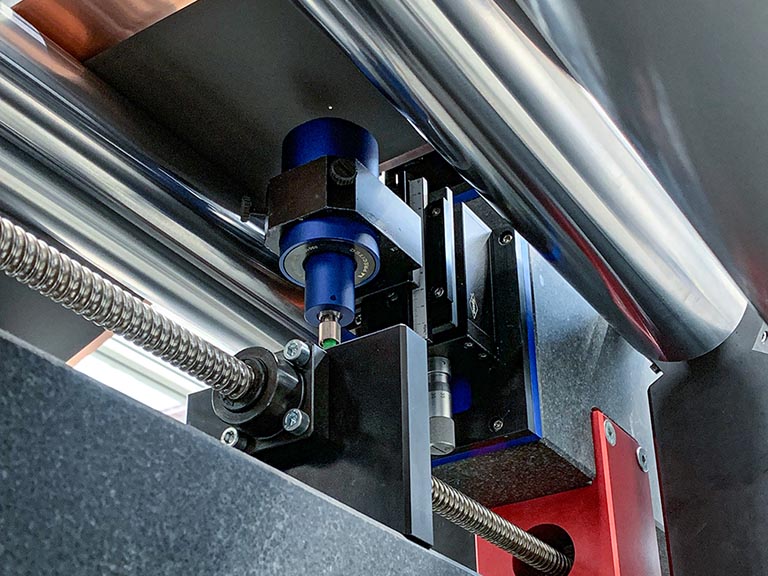
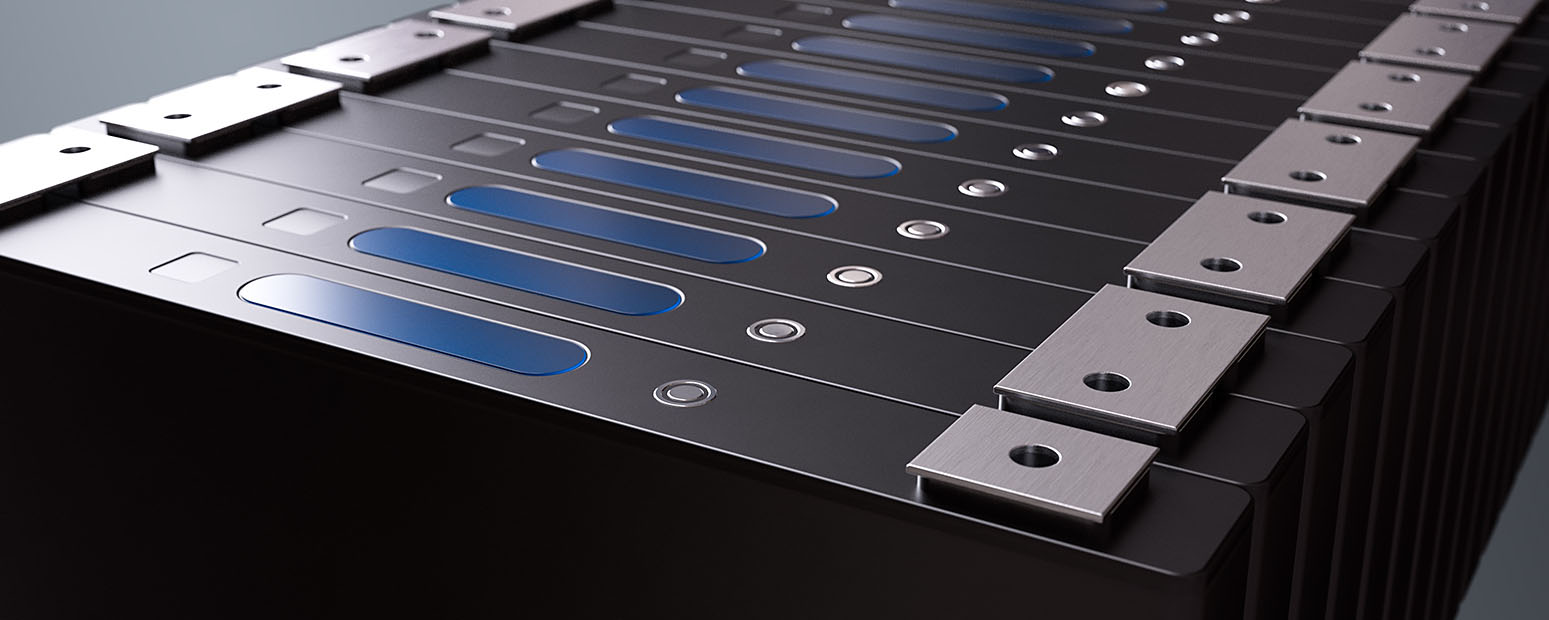
Efficient solutions for the production of lithium-ion battery cells
In electrode production, battery cells are made up of alternating layers of anode and cathode foils. They are separated by the so-called separator. The stack of foils is then rolled up, packed into a metal housing and the batteries are then securely welded.
Our quality control systems are used in numerous process steps to ensure efficient production of the battery cells. This includes, for example, measuring the electrode foil thickness, checking the cutting burr and laser welding the foil layers (foil-to-tab) and the housing with the lid (cap-to-can).
The clear customer requirement here is accuracy: < 1 micrometer. Our sensors meet this requirement and are optimized for the production environments of battery cells, so-called roll-to-roll applications:
- high track speeds
- vibrating electrode foils
- glossy and black surfaces.
In laser technology, cap-to-can laser welding is a crucial application. The aim here is to detect pinholes or, at best, to avoid them altogether. We have optimized our products and optics specifically for these applications and developed innovative solutions.
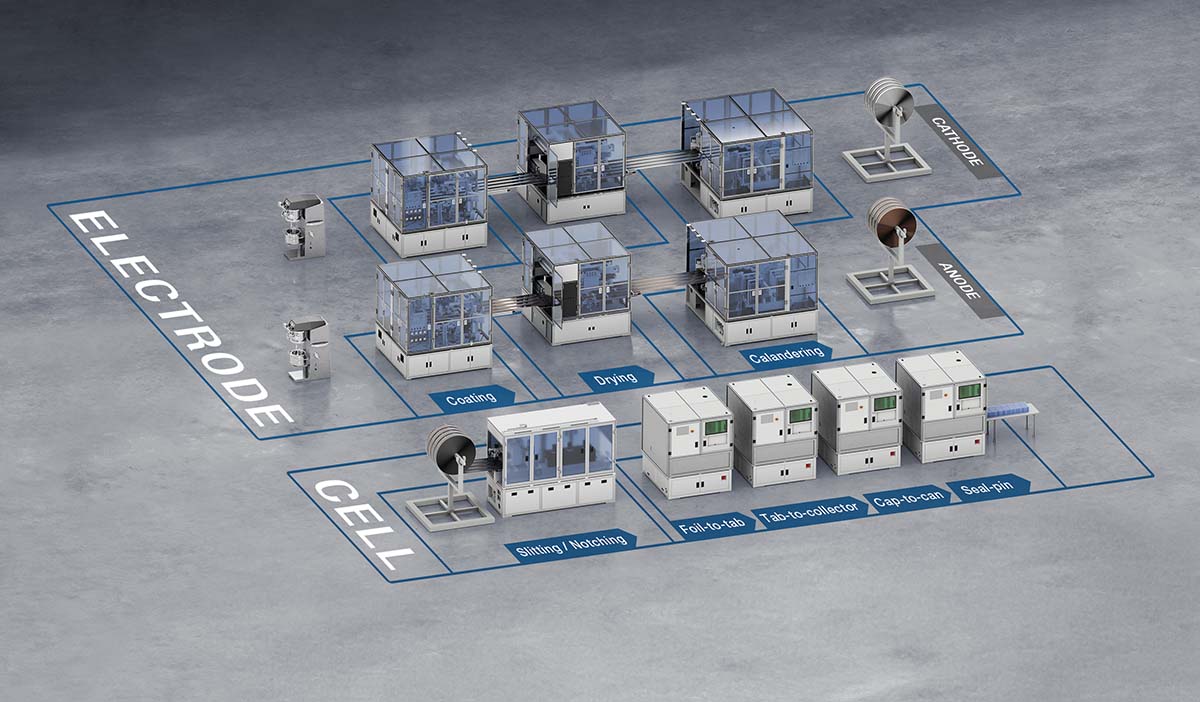
Solutions for your manufacturing steps in electrode production
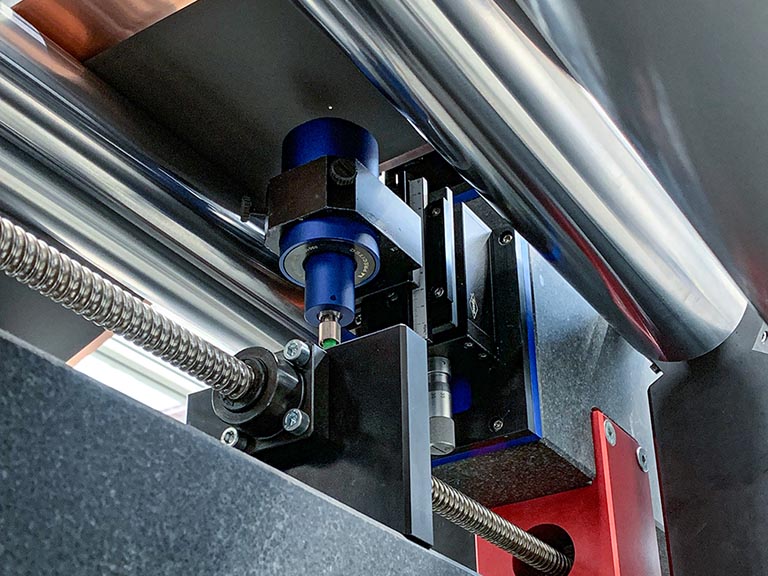
The exact coating thickness of electrode foils plays an essential role, as it has a significant influence on the performance and lifetime of the batteries. In the production process, the carrier film is first coated with the slurry continuously or intermittently and then the solvent is removed from the layer in the drying channel.
Thickness measurements are taken before and after the drying process. The coating can be in a dry or wet state - i.e., our measurement is always exact regardless of whether the surface is reflective, black, or porous. The effects of vibration and belt speed are compensated for. The waviness and thickness of the film are precisely analyzed, and the results are displayed. Current market requirements are an absolute accuracy of < 1 µm in combination with with a repeatability of ± 0.5 µm.
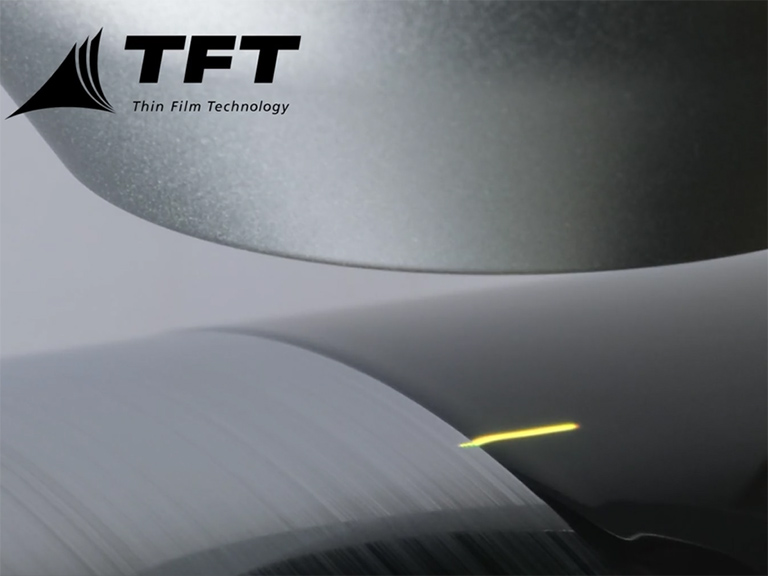
Edge superelevation occurs at the boundary of the applied slurry and can have a negative effect on further processing of the electrode, especially during coiling. It can lead to asymmetrical winding and thus also to massive handling problems.
To increase the performance of battery cells, attempts are currently being made to increase the thickness of the coating. However, thicker coatings also tend to form edge superelevation.
Our line sensor enables precise measurement of the edge over a length of up to 20 mm during the manufacturing process. Both wet and dry edges can be detected. The vibration of the foil is calculated in the process. Transitions from reflective, metallic carrier foils to black slurry can be precisely displayed.
The start/stop edge occurs during intermittent coating. In this process, slurry is alternately applied to the carrier foil or deliberately left out. The start/stop edges are challenging with this type of coating and must be monitored to ensure long life and safety of the battery cell.
With our point sensors, the topography profile can be precisely measured, and thus possible coating defects can be detected early and accurately.
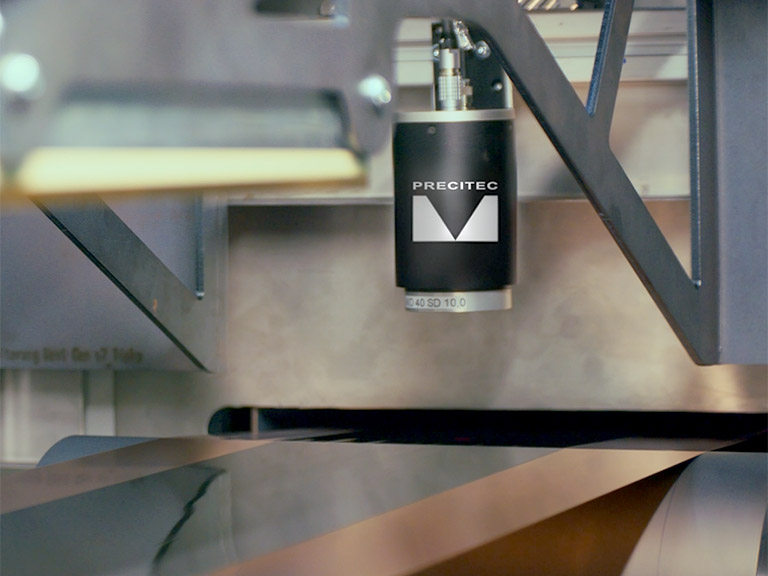
The drying of coated battery foils is a key process step in electrode manufacturing. Due to its high energy requirements, this step offers considerable potential for cost reduction and reduction of the CO₂ footprint – regardless of whether drying is carried out convectively, laser-based, with infrared emitters, or using hybrid processes.
In addition to the energy aspects, the drying process also has a decisive influence on electrode quality. The section from the start of pore emptying is particularly critical: if drying is too intense during this phase, capillary forces can pull the binder to the surface of the slurry. The result is binder migration, which prevents the active material from remaining firmly bonded to the current collector – a risk to the performance and service life of the battery.
Our sensor technology makes it possible to clearly identify the five characteristic stages of the drying process. Through inline integration into roll-to-roll processes, the current drying status can be precisely determined and the process can be specifically controlled. This leads to a significant reduction in energy costs, a sustainable improvement in product quality, and overall higher process reliability.
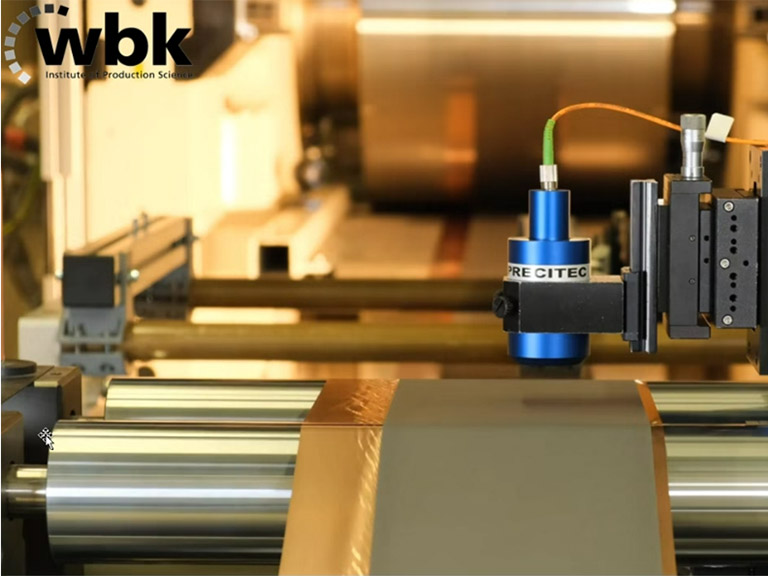
Calendering is the last process step in the production of the electrode. This is where the final thickness and porosity of the coating are essentially determined. Besides the weight per unit area, these are decisive characteristics for the performance and safety of the battery cell.
Our sensors allow comprehensive measurement of the calendering process. The thickness of the electrode before and after calendering, the concentricity of the calender rollers and the so-called wrinkles are measured. These are wrinkles at the edge of the coating on the substrate. Vibrations of the foils are compensated by our sensors and waviness is calculated. This means that exact measurements can be carried out at any time, even at high belt speeds of between 100 - 150 m/min.
Calender rolls are solid steel rolls with diameters larger than 1 m. The mirror-like surfaces are precisely ground to ensure the highest quality of the rolled electrodes. Defects on the rolling surfaces as well as small deviations of the concentricity have a direct influence on the thickness and condition of the electrode foil. Monitoring the wear of the calender roll surfaces as well as the concentricity is therefore of utmost importance.
Our sensors allow these quality characteristics to be recorded. The smallest deviations from concentricity are detected, the smallest scratches on the roll surfaces are detected.
During calendering, the roller forces apply pressure only to the coated areas of the electrode, leaving the uncoated edges unaffected. This difference in pressure can cause wrinkles to form in the battery foil.
Wrinkles, often referred to as "fish bones," result from residual stresses in the material. These are significant defects in electrode production and can seriously affect later manufacturing stages. For instance, additional stress may develop during the winding process, potentially leading to cracks in the electrode.
Our sensor technology can detect wrinkles and measure their size. If they are too large, the material will be rejected. The formation of wrinkles can also be reduced by adjusting the rolling parameters, such as increasing the temperature of the calendar rollers or increasing the web tension.
The separator foil separates the two electrode foils, i.e., the anode and the cathode, and thus prevents short circuits. Separator foils must be electrically insulating and therefore usually consist of porous, sometimes multi-layered plastics such as polypropylene or polyethylene. These films have thicknesses between 15 and 25 µm and must not be damaged by foreign particles. If the separator foil is penetrated, there is a short circuit and the risk of fire ignition is high. (thermal runaway).
With our sensors, we can measure the thickness and integrity of separator films and resolve the thickness of the individual layers.
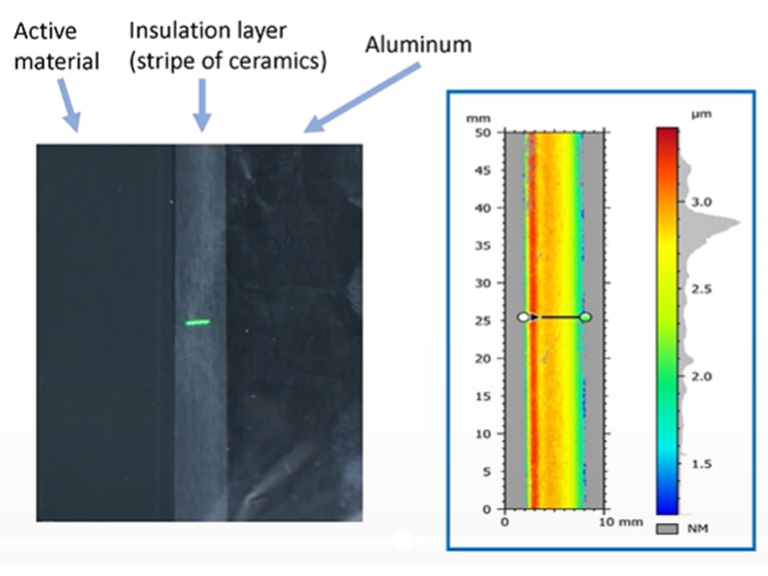
To improve the safety of battery cells, an insulation layer is sometimes applied to the electrode. This consists of a ceramic strip that is applied next to the active material.
The reason for this is that polypropylene separators contract at temperatures of 110°C and even melt at 150°C and above. The ceramic strip prevents the potential risk of a short circuit between the cathode and anode, thereby increasing the safety of the cell.
Standard market thicknesses of the insulation layer are between 3 and 10 µm. For the best quality and efficient production, these are measured inline in roll-to-roll processes - even at high strip speeds of up to 150 m/min. For example, the thickness profile of aluminum oxide (Al2O3) can be displayed and defects detected. A possible gap between the active material and ceramic strip is detected and an overlap of ceramic over active material can also be visualized.
Solutions for your manufacturing steps in cell production
Precitec developed an advanced gas-assisted laser slitting on a slitted roll solution designed for the high-precision cutting of electrode foil. This innovative method ensures consistently high cutting quality by precisely guiding the foil during the process and minimizing vibrations. By cutting directly on the roll, we achieve a smaller laser spot size and reduce average laser power, which significantly minimizes the heat-affected zone (HAZ) and enhances overall cut quality.
Gas-assisted laser cutting also offers a cleaner, more efficient process. Debris and particles generated during cutting are directed into the slitted roll and safely extracted through an integrated system— This prevents contamination of the laser slitting system.
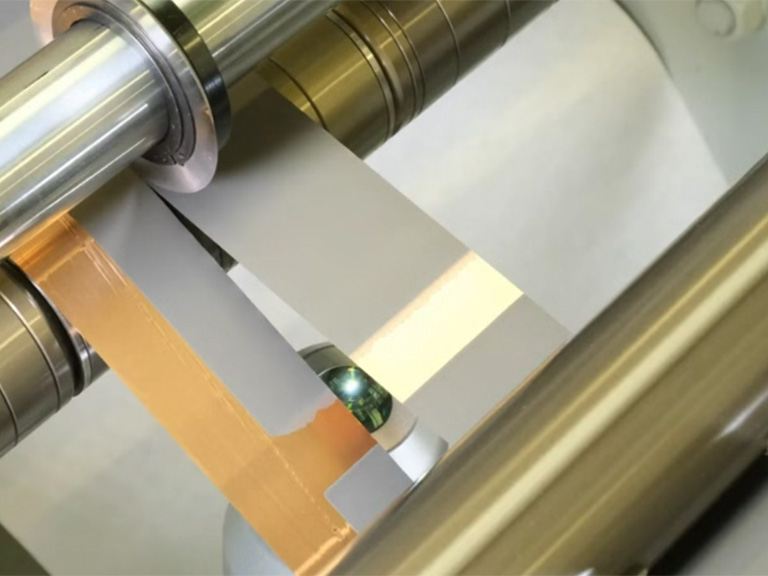
If the separator is penetrated, a short circuit occurs and the risk of fire ignition is high (thermal runaway). Separators usually have a thickness of approx. 20 µm. Therefore, it is of utmost importance to detect cut burrs of approx. 10 µm.
The measurement of the burrs can show the geometry and shape of the metal foils as well as the topography of the coating including the underlying metal foil. Different techniques are used to measure the burrs either from below or from the side, depending on the task and requirements. Integrated into a roll-to-roll system, we therefore reliably detect burrs and thus provide information on the quality of the slitter (predictive maintenance) or the laser cut.
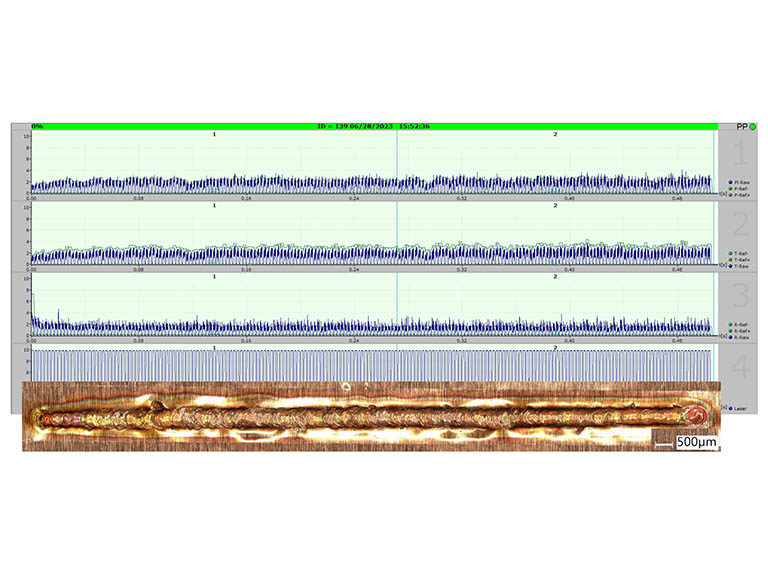
Battery cells consist of several layers of thin copper foils and aluminum foils (5 - 10 µm) that must be welded together to create a stable and powerful battery. Usually 60 - 100 foils are welded together in the process. Depending on the desired capacity and performance of the battery, several of these layers are then stacked on top of each other.
When welding the foil stack, an intelligent welding strategy is important in addition to precise clamping of the foil stack. This makes it possible to realize a secure connection from the first to the last film with little distortion and without burn-through. By using process monitoring systems, welding anomalies and the smallest deviations can be detected to ensure the quality and reliability of the weld seam. Ultimately, this leads to higher production output and better product quality.
Cap-to-can laser welding involves welding a metal lid (cap) onto a metal container (can). This type of laser welding is often used in battery production to isolate the electrolytes from the outside world and to prevent leakage of liquids. Materials here are aluminium or nickel-plated steel.
Cap-to-can laser welding is used for cylindrical but also for prismatic battery cells. In both cases, the quality of the weld is crucial for the performance and reliability of the battery.
With large battery cells, such as the 4680, the roundness of the can is not always 100%. However, it is essential for the tightness of the weld that the laser beam is guided along the contour of the can. The real contour can be measured exactly and quickly with the ScanMaster and the laser beam can be adjusted accordingly. In this way, high-quality weld seams can be achieved without welding into the cell.
A typical defect in cap-to-can laser welding is the so-called pinhole, which can lead to leakage of the welded joint. Large pinholes can be detected as a welding anomaly with the Laser Welding Monitor. The smallest defects on the weld seam are detected in the post-process by measuring the topography of the weld seam. Reworking of the cell is then possible, reducing scrap.
During the assembly of the battery cell, the electrolyte is filled and distributed evenly and completely into the cell to ensure optimum performance. Residues of electrolyte on the outside of the battery cells compromise product safety. The more batteries are produced, the more urgent the need for automated detection and ejection of contaminated areas on the filling side of the battery cell in the production line. In the subsequent process, known as seal pin welding, the filling opening of cylindrical or prismatic cells is seal-welded by laser. Residues of the electrolyte influence the quality of the weld seam and can lead to leaks or considerable contamination by weld spatter. The cell would then be leaky and thus a reject.
After filling the battery cell with the electrolyte, the filling opening is closed with a cover and tightly welded with laser light. This seals the cell and prevents the electrolyte from escaping. The cell is thus sealed.
The welding of battery cells is a critical process step, as it is a tightness welding. If the cell is leaky, it is scrap. Impurities or spatters could lead to tiny leaks in the weld. Precise and spot welding of the seal pin is therefore of great importance to ensure that the cell remains sealed, and no electrolyte can leak out. The goal is distortion-free and tight seams with low and locally limited heat input. Each individual weld can be monitored, evaluated and documented online. Our systems detect irregularities and faulty welds. 100% traceability and transparency of your processes is ensured.
Different cell types for different applications
Three types of lithium-ion batteries are generally used in e-mobility. The batteries work according to the same functional principle and have a high energy density to ensure a long range. Pouch cells, cylindrical cells and prismatic cells are used, which are then connected to form battery modules to be able to provide the necessary power. But how do these cell types differ?
Further fields of application in e-mobility
Fuel cell
A fuel cell consists of numerous bipolar plates that have to be welded gas-tight. In most cases, the welding speeds are very high - as are the quality requirements for the weld seam. In addition, the geometric parameters of the bipolar plates must be precisely maintained to ensure high fuel cell performance. We measure these with our 3D measurement technology sensors.
Powertrain
The electric drive strand consists of the stator, rotor and power electronics, among other things. For high-quality laser welding of stators (hairpin welding), well-stripped hairpin wires are crucial. We can detect varnish residues on wires as well as enable adaptive laser welding processes.