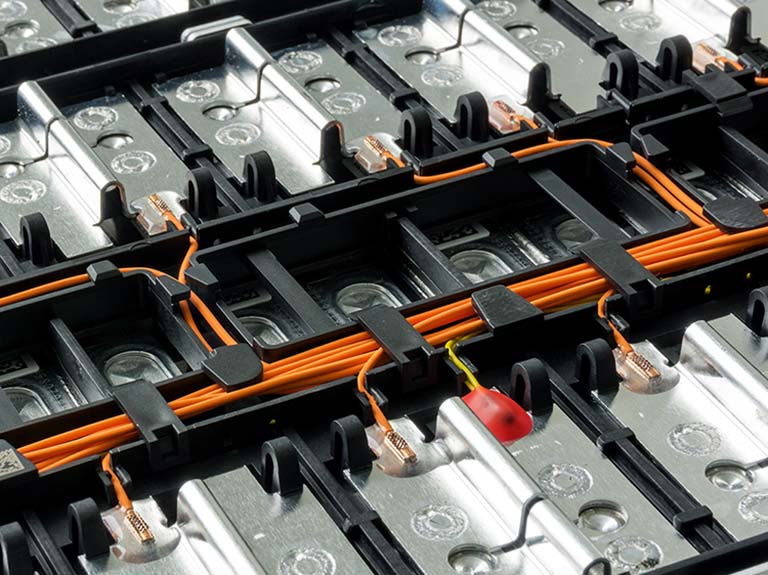
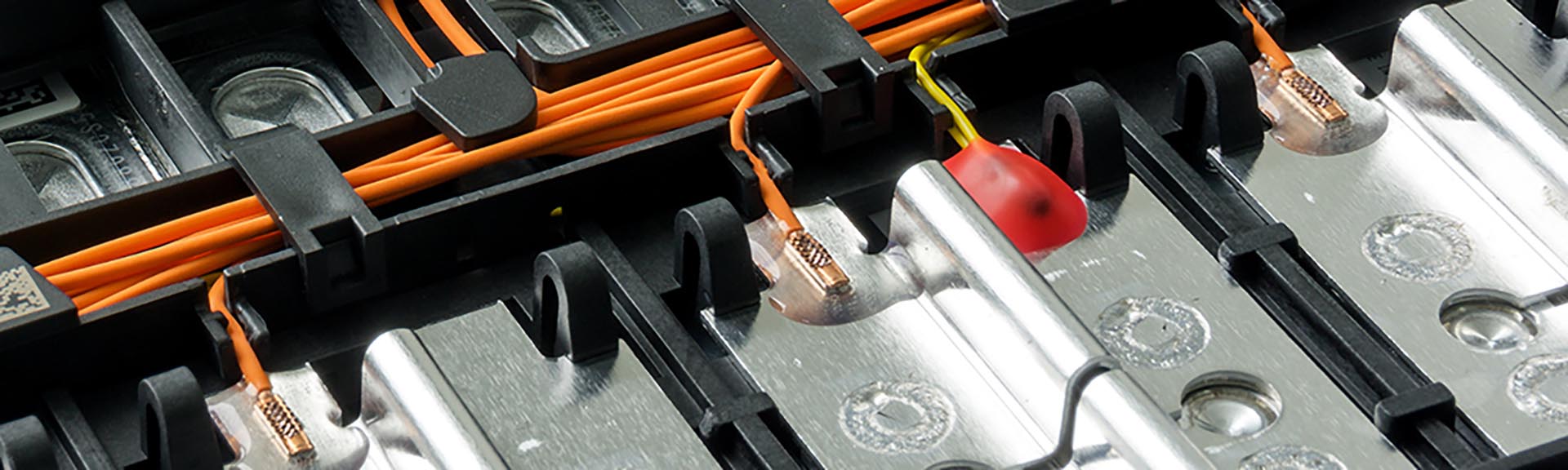
Safe and reliable cell contacting: Innovative solutions for battery module production
Starting with individual battery cells, the process chain continues with the manufacture of battery modules. These are then grouped into a metal frame made of aluminum or steel, the so-called packs, and then bonded to the battery tray.
Among the above-mentioned process steps, there is one critical process that is relevant to safety: the contacting of the individual battery cells. Here, it is important that the cell connector is securely welded to the individual cells. This involves an I-seam at the overlap joint. This connection is treacherous because it is not possible to visually verify whether the two sheets are connected. This is referred to as the "false friend" type of defect.
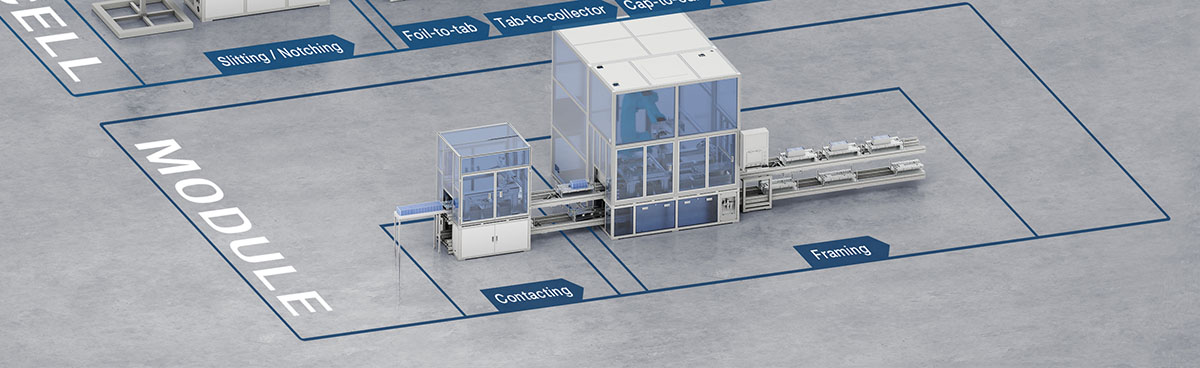
Solutions for your production steps in battery module manufacturing
To deliver a high-quality component that withstands mechanical loads, meet the weld joint standard requirements, avoid weld joints breaking or cracks appearing, and comply with product specifications, several features of weld joints have to be checked. Any pinholes must be detected because tightness is crucial, the seam underfill inspected for resilience to mechanical loads, the seam undercut to prevent notch effects and cracks, and the seam width to control the focus position.
The solution to all these challenges is our CHRocodile CLS 2 line sensor, which can measure the entire topography in one line – even for features tinier than 5 µm – at a high measuring speed.
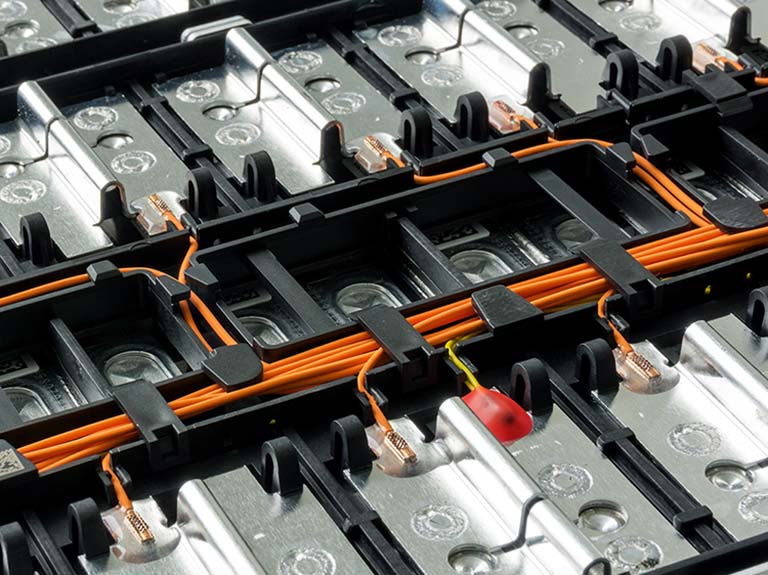
Whether cylindrical, prismatic or as a pouch - the precise and accurate production of battery cells is a decisive factor for their performance and quality. The laser works contactless and is a safe tool for this purpose. When contacting the battery cells with each other, distortion-free seams are created with low and locally limited heat input. Each individual welded contact can be monitored, evaluated, and documented online. Our systems detect anomalies and faulty welds. Non-conforming parts can be re-welded. This enables 100% traceability and transparency of your processes. Costs and quality of your cell production can thus be optimized.
A critical defect in the contacting of battery cells to cell modules is the so-called "false friend": From a purely visual point of view, the weld seam looks good, but there is no electrical contact. The detection of these defects with quality monitoring systems is therefore essential.
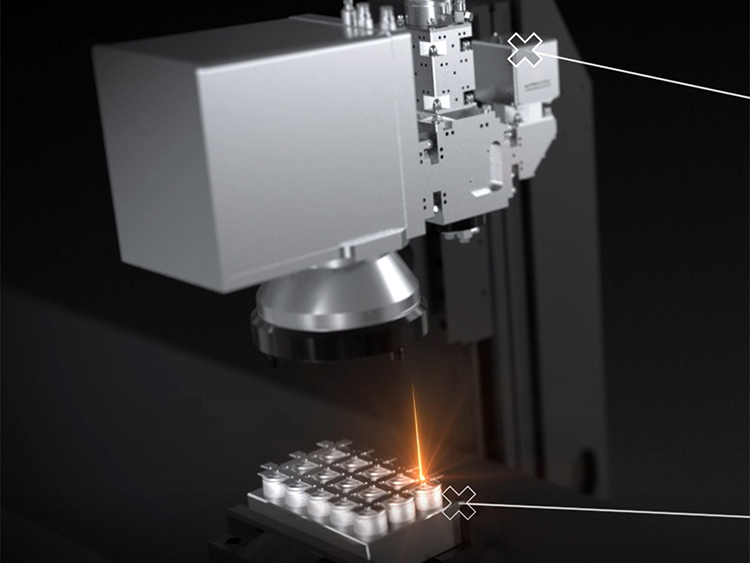
In classic round cells, the cylindrical battery cells, electrode foils are rolled up and sealed in a metal housing. In a downstream step, the cells are contacted with each other so that they can later deliver their full performance. When contacting cylindrical cells, the laser welds very thin layers between 100 and 400 µm. The precise and reproducible processing of these is essential and, in combination with online process monitoring, increases the process reliability of your production line. Costs, quality, and throughput of your cell production can thus be optimized.
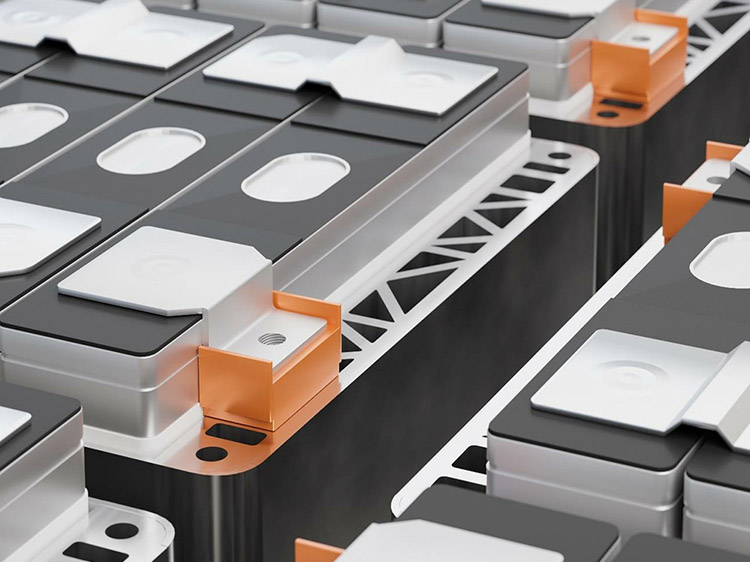
E-mobility battery packs are increasingly being painted with UV-cured or epoxy paints. The thickness of this paint needs to be measured, as it is a mandatory requirement and especially important in critical areas like pack angles. Unfortunately, the existing contact measurement technologies only offer low repeatability levels and are highly operator dependent.
The ideal solution for measuring the paint coating thickness on battery cells is laser photothermal technology from Precitec Enovasense, which enables entire surfaces to be measured with an outstanding level of precision. This technology allows non-contact, non-destructive, non-intrusive, non-radiative measurements of paint coating thickness with an outstanding level of repeatability in a fast and cost-effective process. You benefit from improved process quality through in- or off-line measurement from a compact, lightweight device that is easily integratable into your production processes. Multiple measuring points can be covered in seconds through pre-programmed cycles if the sensor is embedded in the fully automated 3-axis control station HKL2.
Detailed information can be downloaded by filling out the form.
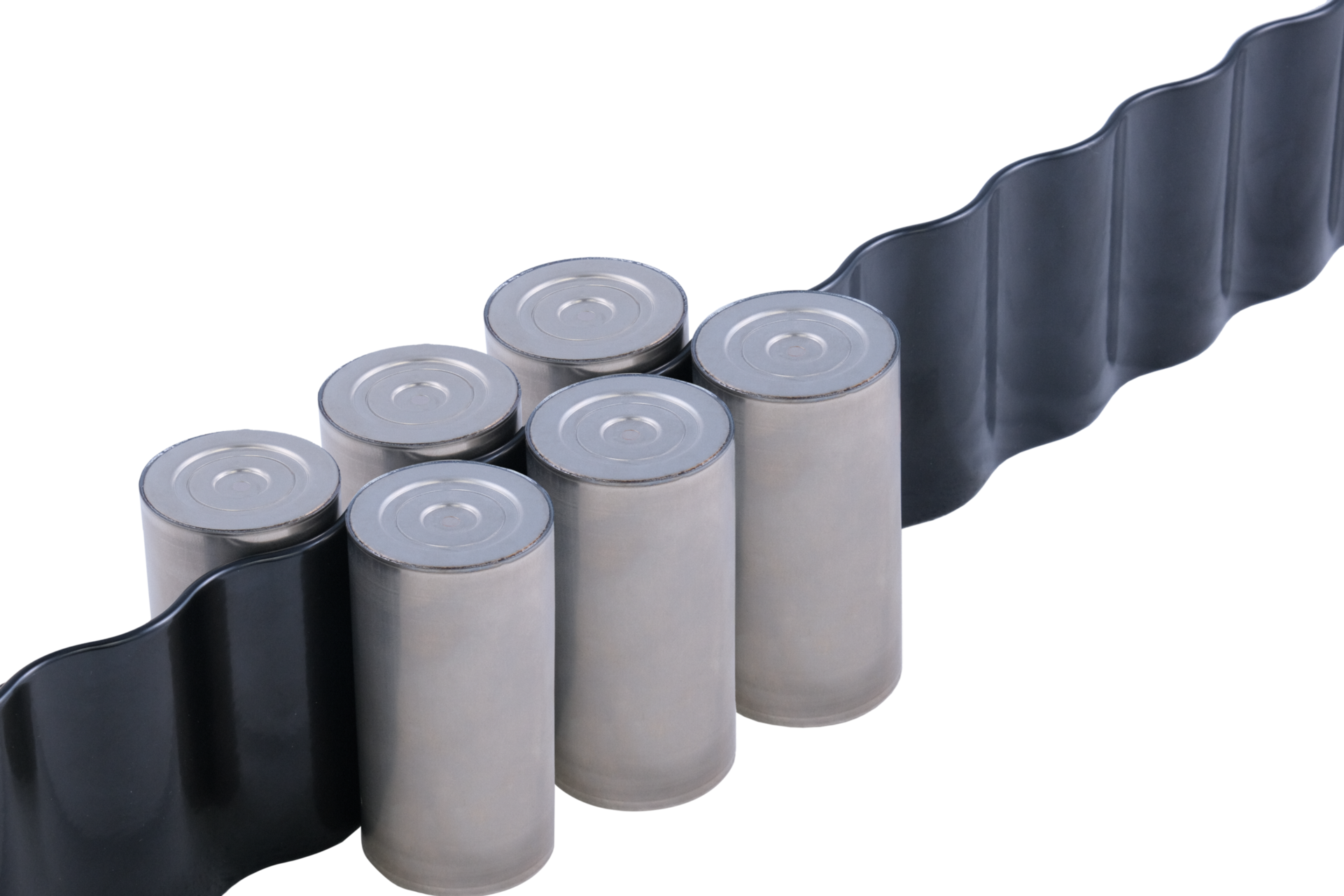
The performance and lifetime of battery cells depend heavily on the operating temperature. Efficient thermal management is therefore required. So-called cooling plates or cooling channels, help to keep the operating temperature of the batteries in the optimum range.
Coolant ducts inside the cooling plates, allow the coolant to circulate and carry out the heat.
The cooling plates, usually made of aluminum contain coolant ducts in which the coolant circulates and carry out the heat. Uniform and full-surface contact is important here. Insulation layers are used to electrically insulate the battery and cooling plate from each other, thereby preventing short circuits and ensuring safety.
Whether the layers are transparent or non-transparent – the Precitec point sensors offer the possibility of measuring these layers.
Would you like to learn more about measuring transparent layers? Click here
Would you like to learn more about measuring non-transparent layers? Click here
In the following step, individual battery modules are combined into battery boxes. Due to desired weight reductions of car bodies, these consist of high-strength aluminum alloys of the 5xxx and 6xxx series. Hot cracks and spatters are the biggest challenge at this point. Therefore, the use of highly accurate quality monitoring systems is essential for the low-crack and low-porosity laser welding of aluminum structures.
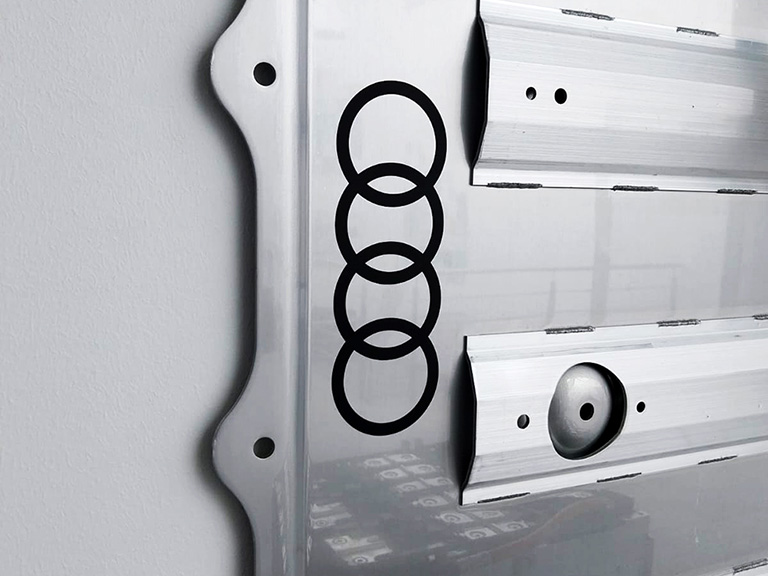
The battery boxes are placed on the underride guard over the entire surface during the production process. Partial reinforcement by welding on high-strength materials ensures a permanent hold and resistant protection of the battery modules. Intelligent and automated laser welding systems are convincing here due to the highly dynamic beam guidance, the targeted reduction of heat input and thus the optimal shaping of your weld seam. The joint seam is evaluated immediately after the laser welding.
Further fields of application in e-mobility
Fuel cell
A fuel cell consists of numerous bipolar plates that have to be welded gas-tight. In most cases, the welding speeds are very high - as are the quality requirements for the weld seam. In addition, the geometric parameters of the bipolar plates must be precisely maintained to ensure high fuel cell performance. We measure these with our 3D measurement technology sensors.
Powertrain
The electric drive strand consists of the stator, rotor and power electronics, among other things. For high-quality laser welding of stators (hairpin welding), well-stripped hairpin wires are crucial. We can detect varnish residues on wires as well as enable adaptive laser welding processes.