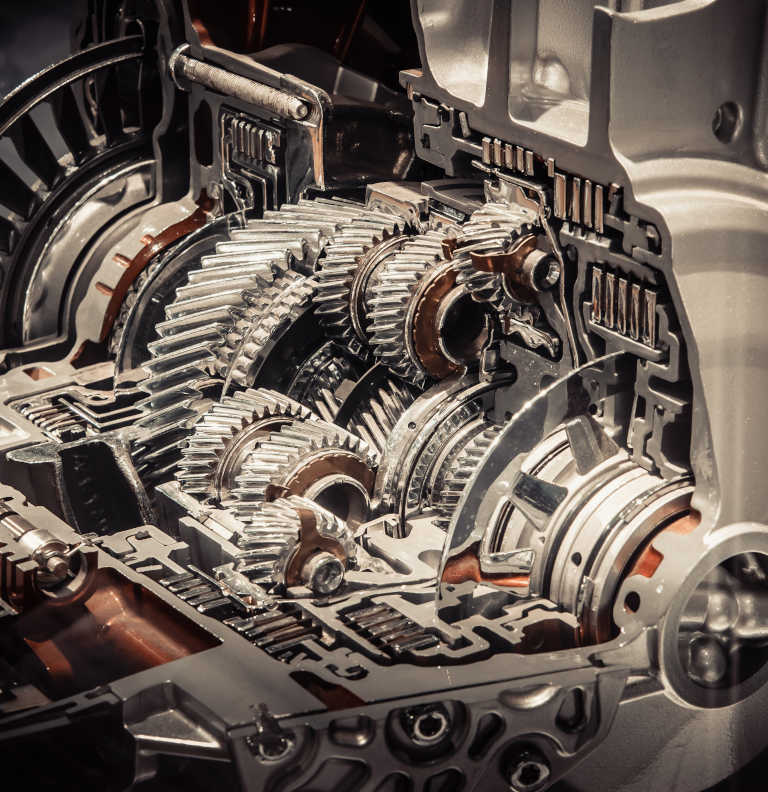
Laser welding in gear production
Automation increases your process quality
Modern transmissions have 8 to 10 gear teeth. And as modern design has improved, components have decreased size. Therefore, the installation space required for this in the car has decreased as well. The development of gear production to today's size and performance is in many ways due to the laser welding.
Here the laser represents an "enabling technology". Hardly any other joining method can join components in such a small space with such precision and high strength. In order to be able to exploit the strengths of the laser, it is important to hit the joining point exactly. An offset of only 0.1 mm can lead to failure of the component.
The WeldMaster 4.0 Track is able to find the joining position contact-free, which allows it to position the laser beam with the necessary precision. All data is recorded and position errors are immediately transmitted to the system. The use of the system increases the output of your welding system on "IO-parts" and documents the produced quality.
The use of Precitec IDM is also industry proven. The system complementarily measures the welding depth of each welded part throughout the entire weld. The 100% inspection significantly increases production reliability and allows faulty welds to be detected early on.
The measured values are analyzed and saved in the WeldMaster 4.0 Track System together with the positioning data. The measuring principle is online and non-destructive, which increases the output of the system and noticeably reduces the number of test parts.