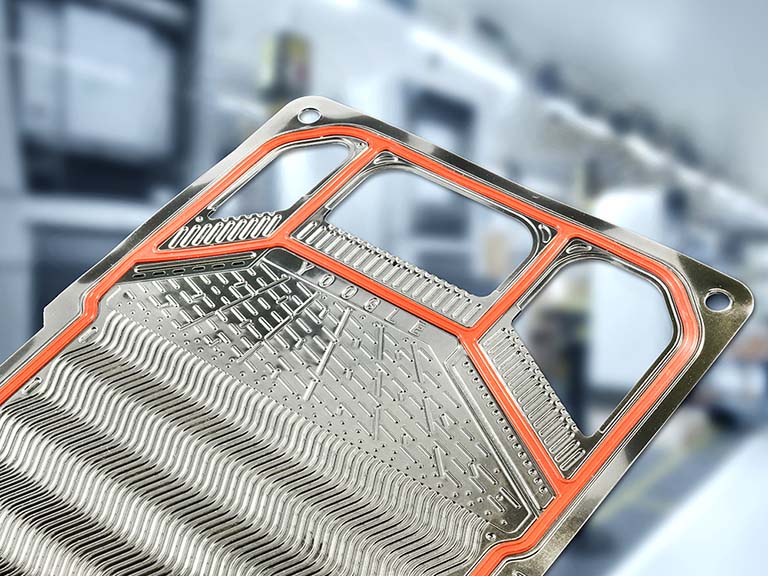
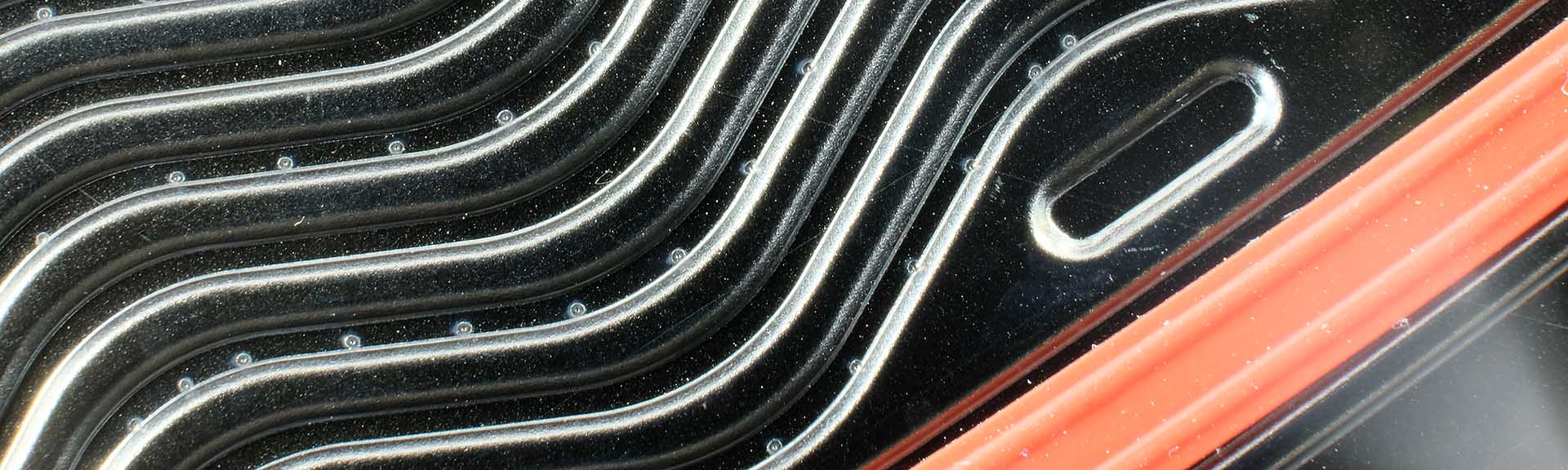
Innovative 3D measurement technology and laser cutting optics for precise fuel cell production
The energy in an electric vehicle comes either from a battery - or from a fuel cell. Fuel cells consist of a stack, which means they are built up in layers. The individual elements are bipolar plate, gasket, gas diffusion layer (GDL) and membrane electrode assembly (MEA).
Regardless of whether metallic or graphite bipolar plates are used, the requirements for our 3D measurement technology are similar. It is a matter of the exact measurement of geometric parameters such as channel depth and channel spacing, the position of the channel web, the roughness of the channels or the determination of thicknesses of plastics or metallic layers. Especially for the determination of layer thicknesses we can rely on different technologies to analyze transparent as well as non-transparent layers.
Metallic bipolar plates are thin sheets with a thickness of about 50 - 75 micrometers and are usually punched. However, small holes on the plates are cut by laser and here our laser cutting optics are used. Furthermore, individual bipolar plates are welded together. Depending on the size and number of bipolar plates, a fuel cell can therefore contain about 500 m of laser welds. Monitoring the welds and their quality is therefore an essential step for the mass production of fuel cells.
Solutions for your production steps in fuel cell manufacturing
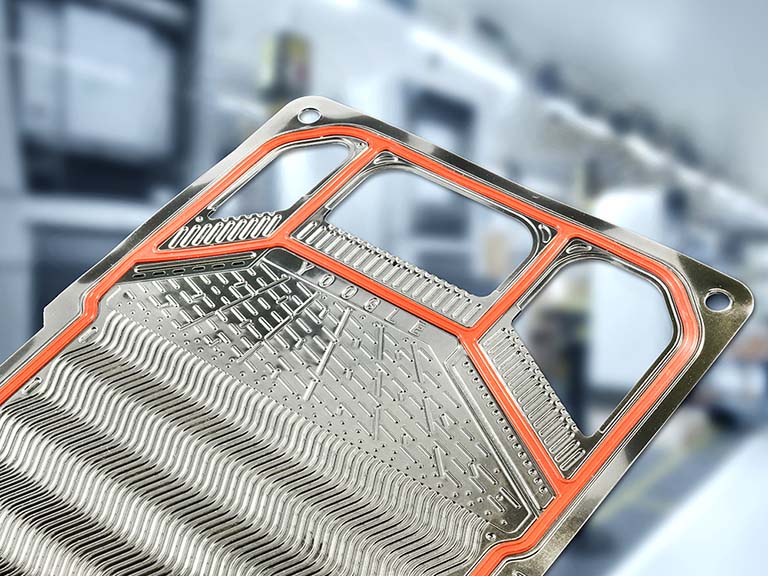
Bipolar plates are an important component in fuel cells, separating the electrodes and the electrolyte and at the same time conducting the current between the electrodes. Two plates each with a thickness of between 50 and 100 microns must therefore be welded together in a gas-tight manner to form a stable and conductive structure. They are often made of metal, such as stainless steel.
When joining the contact surfaces of the thin plates, the weld is usually very narrow and deep, resulting in a high strength and conductivity of the weld. The laser weld can be in various forms, such as a spot (step or contacting seam) or line (sealing seam).
Approximately 1 m of weld is required per bipolar plate. A stack consists of approx. 400 bipolar plates and therefore has 400 m of weld seam, which must meet the highest quality standards. It must be tight. In order to enable high cycle times, welding is also carried out very quickly at approx. 600 - 800 mm/s, i.e. just below the so-called humping limit. During the welding process, careful monitoring and control of the process is required. Our sensors detect the smallest welding defects that can lead to leakage at the sealing seams. In addition, the monitoring system takes into account the high welding speeds of the sealing seams or the short welding durations of the contacting seams. We sample with a sampling rate of up to 250 kHz.
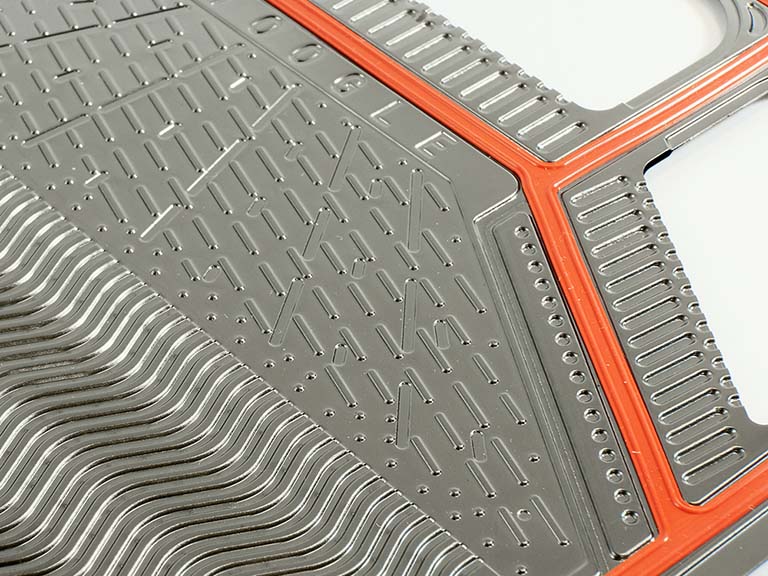
Small dimensions, high accuracy requirements, and critical cycle times are some of the key challenges in measuring fuel cell topography. The dimensions of bipolar plates need to be measured to guarantee dimensional tolerance, because the quality of the bipolar plates is crucial for a fuel cell’s efficiency and power density. The parameters that need to be monitored are the sheet thickness, depth and width of channels, channel center distances and precise design requirements.
To master these measurement challenges Precitec offers three assignment-specific solutions: the CHRocodile 2 DPS for thickness measurements;
the CHRocodile CLS 2 for ultra-precise 3D profile inspection;
and the Flying Spot Scanner 310 for geometry/shape measurements. Thanks to the latter’s movable point, it can measure exactly the path required – even on big plates – with no need to move the sample.
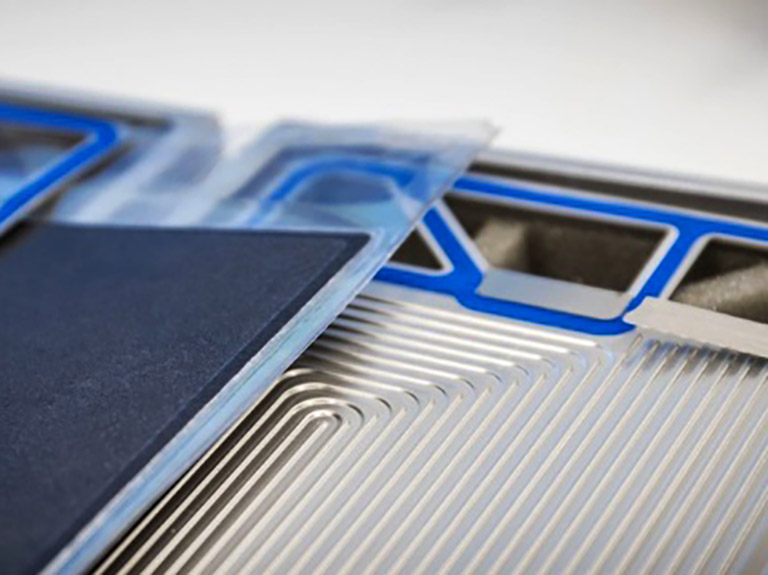
The challenge here is to accurately measure the thickness of metallic (gold or titanium) coatings on bipolar plates. These coatings have to have exactly the right thickness to avoid corrosion and ensure high electrical conductivity.
The ideal solution for measuring bipolar plate coatings on fuel cells is laser photothermal technology from Precitec Enovasense, which enables entire surfaces to be measured with an outstanding level of precision. This technology allows non-contact, non-destructive, non-intrusive, non-radiative measurements of metallic coatingthickness with an outstanding level of repeatability in a fast and cost-effective process. You benefit from improved process quality through in- or off-line measurement from a compact, lightweight device that is easily integratable into your production processes. Multiple measuring points can be covered in seconds through pre-programmed cycles if the sensor is embedded in the fully automated 3-axis control station HKL2.
Detailed information can be downloaded by filling out the form.
Further fields of application in e-mobility
Powertrain
The electric drive strand consists of the stator, rotor and power electronics, among other things. For high-quality laser welding of stators (hairpin welding), well-stripped hairpin wires are crucial. We can detect varnish residues on wires as well as enable adaptive laser welding processes.