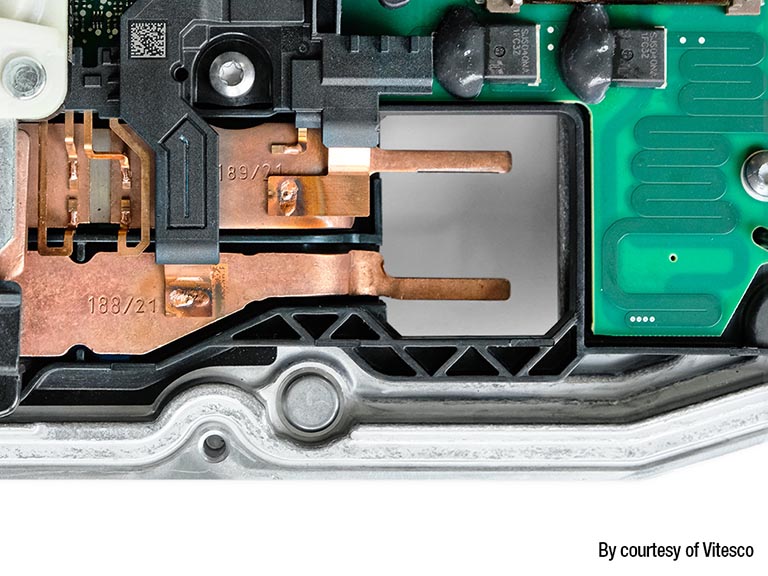
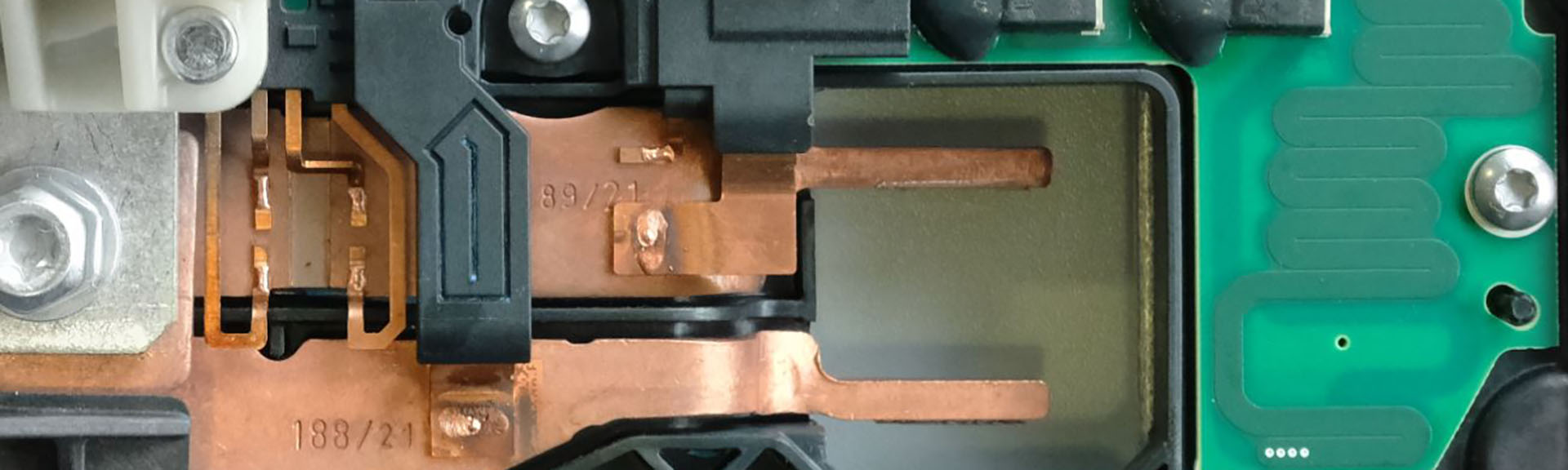
Reliable welded joints for power electronics in electric drives
The power electronics are an essential element of an electric drive. It conducts the traction energy from the battery or fuel cell to the electric motor, converting the current from direct to alternating current.
The components to be welded are mostly copper sheets with thicknesses between 0.5 - 3 mm. Wherever high electrical currents flow, high weld quality is crucial. Welding spatter and thus flying particles could lead to a short circuit and thus to component failure. A high degree of mechanical strength is also required of the weld seam in order to cope with vibrations during operation at the customer's site.
Solutions for your manufacturing steps in power electronics
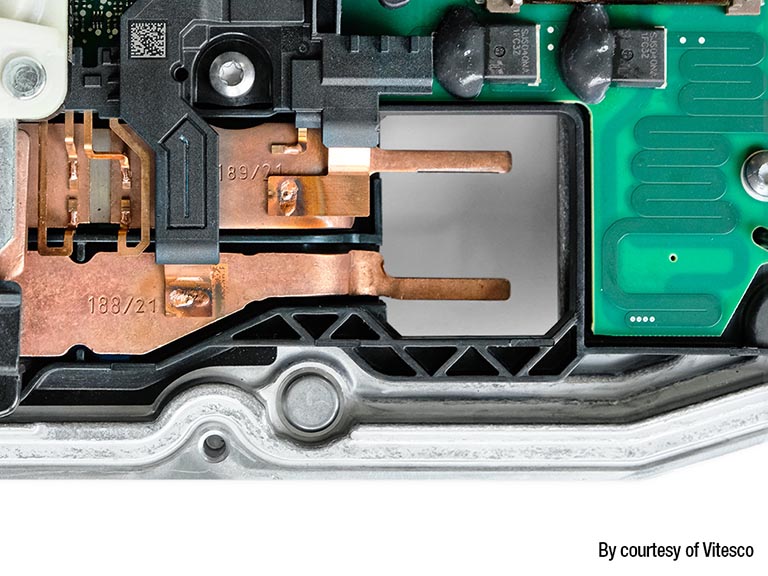
For laser welding of terminal contacts, modern production lines rely on precise and gentle micro welding processes. These are particularly suitable for the pinpoint contacting of electronic components that are thermally sensitive. To ensure consistently high quality and reliability of the welded joints, process monitoring is essential. Welding parameters are controlled in real time and adjusted as necessary to achieve optimum results. This ensures that a perfect welded joint is always achieved, even with high demands on precision and speed.
Laser welding of IGBT (insulated gate bipolar transistor) boards is an important step in the production of power electronics modules. Laser welding technology offers a precise, very fast and automated way to connect the terminals of the IGBT module to the heat sink. Process monitoring is key here, as poor weld quality can cause the module to malfunction. By integrating real-time monitoring, sources of error can be quickly identified and corrected. In this way, a consistently high quality of the welded joint can be ensured.
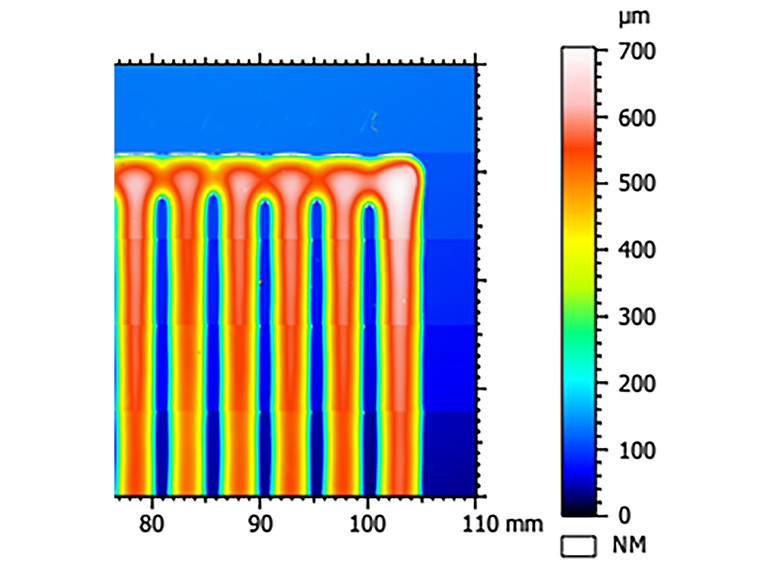
The quality of the housing sealing in the power electronics control units for electric-powered vehicles has to be inspected for sealing tightness. Here, the inspection technology has to check for bubble-free dispensing, non-interrupted gasket deposition, and the required shape, width and position during sealing application.
Our CHRocodile CLS 2 line sensor fulfils all these requirements. It can measure the entire housing of power electronics units with great accuracy and at high speed. Its non-contact, non-destructive measuring technology is ideal, even on high gasket slopes.
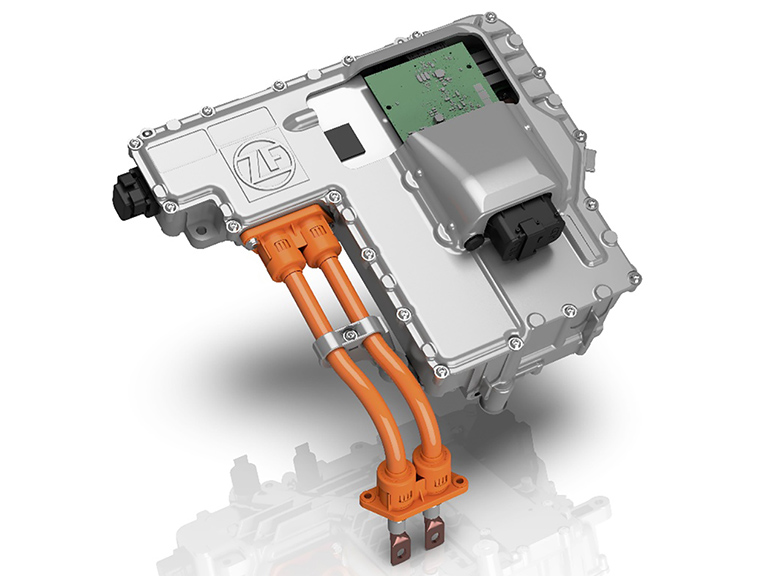
Printed circuit boards (PCBs) are coated with protective lacquers of a prescribed thickness for protection and insulation purposes. Compliance with thickness specifications is essential. The thickness of ultra-thin plastic coatings (15-7,600 µm) has to be measured with the required precision. An additional challenge comes from the customary short cycle times and the measurements required at various locations.
The solution to these challenges is our Flying Spot Scanner 310, which measures ultra-precisely and ensures short cycle times and high throughput.
Highly accurate 3D measurements of wire loop and bond height are required in 3D packaging technology. Topographic inspection of final bonding quality is also vital to ensure the correct functioning of semiconductors. One specific challenge is the ultra-tiny diameters of the wires. What’s more, conventional 2D imaging technology is not suitable for checking the loop height of crossing wires.
The solution we offer for inspecting wire loop and bond height and wire crossings is the CHRocodile CLS 2Pro line sensor, which is ideal for measuring topography in semiconductor applications. The sensor’s ultra-high acceptance angle enables precise topographic measurements of round shapes, such as wire loops and solder bumps, while its fast data acquisition rate of up to 43.2 million pixels per second and 36,000 lines per second ensures short cycle times.
Further fields of application in e-mobility
Fuel cell
A fuel cell consists of numerous bipolar plates that have to be welded gas-tight. In most cases, the welding speeds are very high - as are the quality requirements for the weld seam. In addition, the geometric parameters of the bipolar plates must be precisely maintained to ensure high fuel cell performance. We measure these with our 3D measurement technology sensors.
Powertrain
The electric drive strand consists of the stator, rotor and power electronics, among other things. For high-quality laser welding of stators (hairpin welding), well-stripped hairpin wires are crucial. We can detect varnish residues on wires as well as enable adaptive laser welding processes.