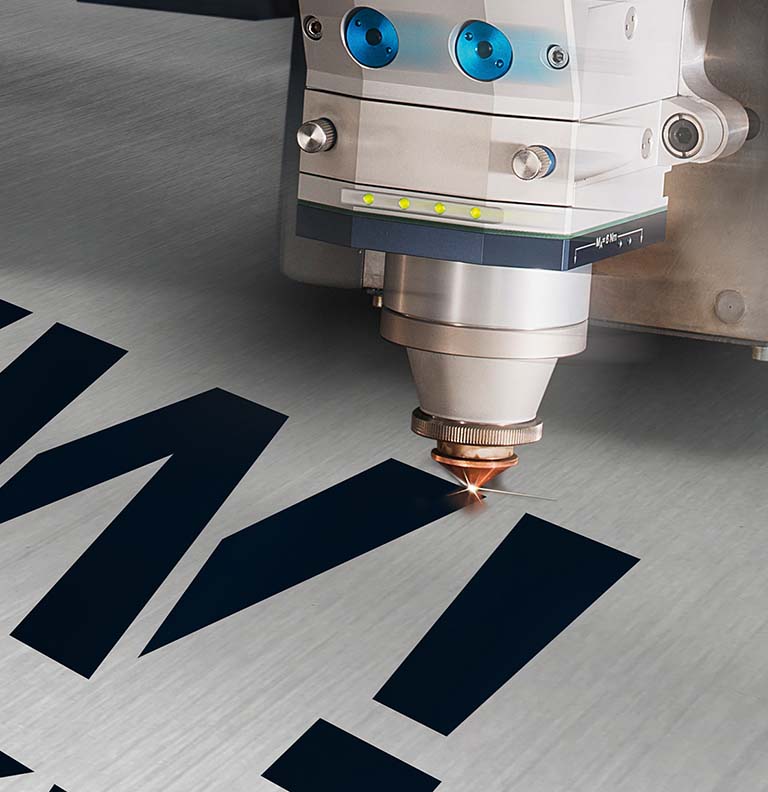
Automation of your cutting processes
Integrated intelligent sensor technology with added value
Our intelligent sensor systems help you to monitor and automate the cutting process. This makes your production task more efficient, transparent, and economical. Various solutions help to ensure that the laser cutting process is permanently stable and precise, to obtain optimized cut qualities and to avoid production rejects.
By far the best sensor
Precise measurement and automated control
The company name Precitec stands for precision and technology. At the beginning of the 1990s, the company's success story began with the first CO2 cutting heads equipped with the innovative, fully automated, capacitive clearance control. The technology was continuously developed and is still the reference in the field of 2D and 3D laser cutting today. In combination with modern solid-state lasers, such as fiber lasers and disk lasers, it impresses with precision and long-term stability. A constant working distance is guaranteed throughout the entire application spectrum: from piercing and high-speed cutting of thin sheets to thick sheets cutting with very high laser power. Because only a constant distance between component and cutting head achieves optimum cutting qualities and highest cutting speeds. Even the smallest deviations lead to burr formation or have an unfavourable effect on the cutting speed, the roughness of the cut surfaces and the gap width.
Additional added value in the process ancillary times
In addition, the distance sensor technology impresses with valuable functions in process ancillary times. While the cutting head is positioned quickly, it acts as a collision sensor and avoids costly mechanical damage. In addition, in flatbed cutting applications, it can detect the edges of the metal sheet and ensure that the material is used particularly economically. The distance sensor technology also shows its strengths in laser cutting of tubes and profiles as well as in robot applications. Manual intervention or additional retraction for batch or profile changes is no longer necessary.
Smart, process stable distance control with CutBox Pro
- Intelligent heart of your cutting system
- Functionalities of Precitec distance sensor technology in a single piece of hardware
- Real-time adjustment of the focus position with BeamTec
- Low installation effort
Distance control with CutBox Pro
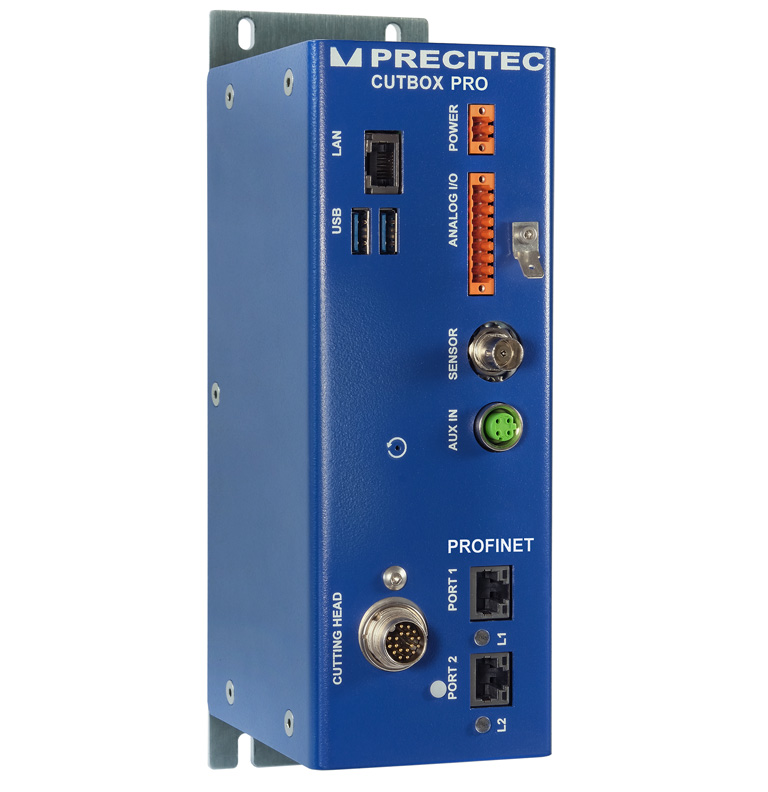
Industry 4.0 and KI
Parallel to the rapidly advancing networking, Precitec is utilizing various development approaches in the field of industrial digitalization. Driven by the joy of innovation, our intelligent cutting solutions help you to automate the cutting process and thus make your production task efficient, transparent and economical.
Clever solutions for networked production
Faster, easier, more enduring - that is the declared goal for the production of tomorrow. New automation solutions make it possible to network the individual production steps intelligently and profitably.
At the beginning of 2019, INCUBATOR was founded in Karlsruhe with precisely this claim. Since then, a young team has been working on concepts for the laser process of tomorrow. Modern IT technologies and methods such as Industrial Internet of Things (IIoT), Machine Learning (ML), Artificial Intelligence (AI) and Cloud Computing form one of the essential cornerstones. Based on artificial intelligence, our systems are continuously developed further and thus, the flood of data is reduced to the relevant level or maintenance intervals are specified in an optimized way.
Always informed, even wirelessly
Smart sensors integrated into the cutting head continuously monitor the status of critical components or cutting process parameters. Clear status signals and error messages are provided for further handling. So-called warning thresholds can also be individually defined and set, allowing adaptation to any system configuration and ensuring that the
cutting process is reliably monitored.
Recorded information is easily and seamlessly integrated into existing data acquisition systems. In addition, it is possible to access the data via mobile devices and to have the current status of the cutting head visualized or to query error messages.
Trust is good, control is better
We test the reliable continuous operation of our new development approaches intensively in our own laser laboratories and cutting facilities. Due to the most modern equipment and very high laser power, we push the limits of the applications.
PierceTec – Piercing process during laser cutting
Increase your productivity - robust and with high quality
PierceTec represents fast, clean and reproducible piercing during laser cutting. The technology doesn't just monitor the piercing process, it also controls it. The piercing time is shortened to a minimum. Only as much laser power is used as the process effectively requires. The result is impressive: the piercing holes are precisely and evenly formed. On the upper side of the sheet metal, significantly less material (ejection) is formed throughout. In this way, you achieve a constant hole and surface quality and can reduce the amount of rework required.
Reduction of time and machine downtime
PierceTec also reliably ensures increased process reliability during the cutting process: in real time, unintended cut breaks are detected and reported to the customer's control system without delay. In the event of inconsistent batch quality or material changes, direct intervention by the machine operator is therefore no longer necessary. Moreover, the PierceTec system protects the usual wear parts such as the protective glass on the process side and the cutting nozzle. The longer service life reduces follow-up costs and the occurrence of machine downtimes.
In summary: PierceTec saves cycle time and operating costs-and simultaneously increases the performance and quality of the piercing process.
Easy integration
PierceTec technology is compatible with all laser beam sources and can be used as a fully integrated sensor in the ProCutter 2.0 cutting head or as a sensor built into the laser source. Predefined programs can be selected, saving time during commissioning.