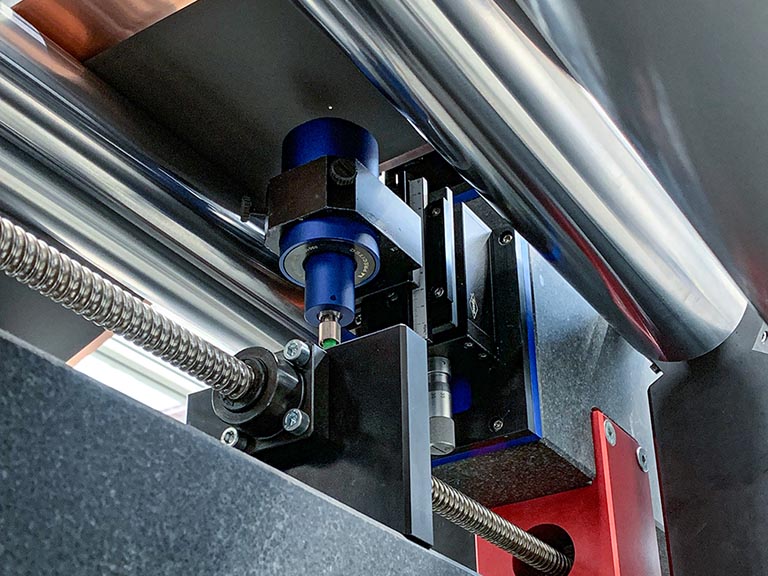
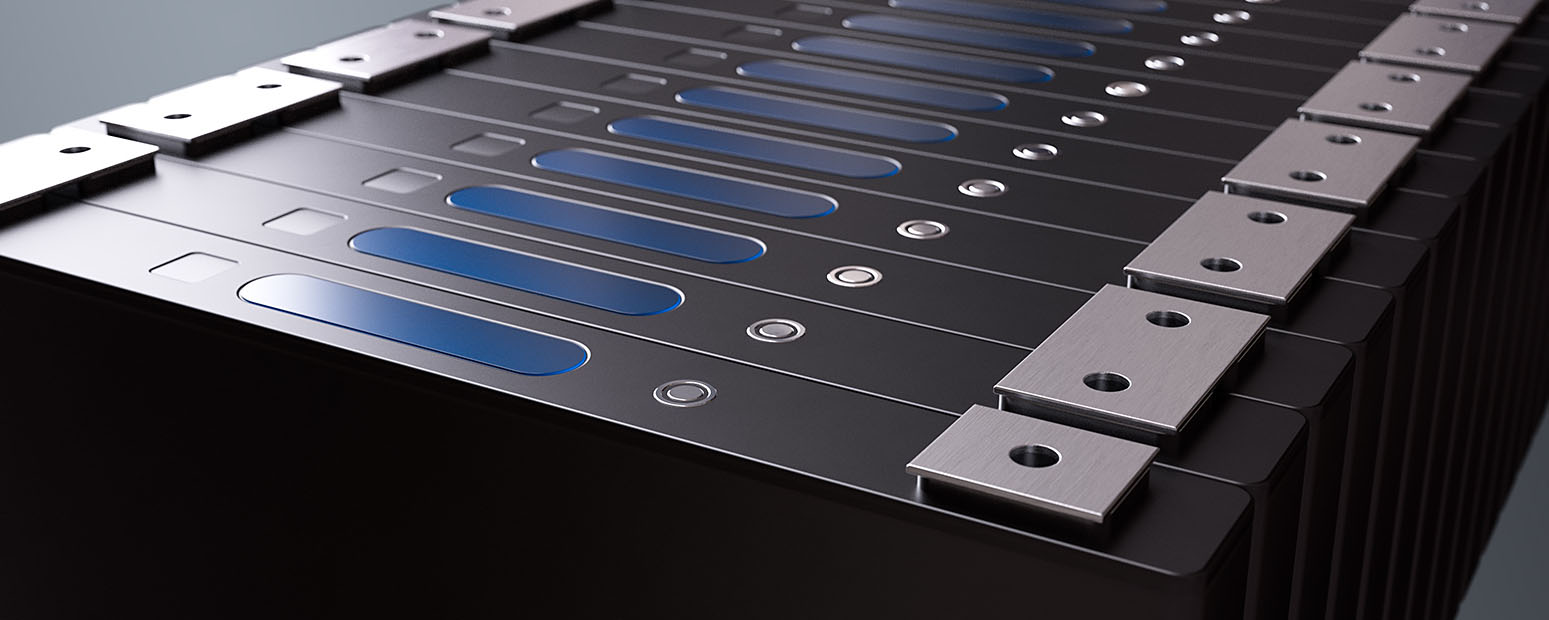
Effiziente Lösungen für die Fertigung von Lithium-Ionen-Batteriezellen
Batteriezellen werden in der Elektrodenproduktion aus alternierenden Schichten von Anoden- und Kathodenfolien aufgebaut. Sie sind dabei durch den sogenannten Separator getrennt. Im Anschluss wird der Folienstapel aufgerollt, in ein Metallgehäuse gepackt und die Batterien abschließend sicher verschweißt.
Für eine effiziente Fertigung der Batteriezellen kommen in zahlreichen Prozessschritten unsere Systeme zur Qualitätskontrolle zum Einsatz. Das umfasst beispielsweise die Vermessung der Elektrodenfoliendicke, die Überprüfung des Schnittgrats sowie das Laserschweißen der Folienlagen (Foil-to-Tab) und des Gehäuses mit dem Deckel (Cap-to-can).
Die klare kundenseitige Anforderung lautet hier: Genauigkeiten < 1 Mikrometer. Unsere Sensoren erfüllen diese Anforderung und sind optimiert auf die Produktionsumgebungen von Batteriezellen, den sogenannten Rolle-zu-Rolle-Anwendungen:
- hohe Bahngeschwindigkeiten
- vibrierende Elektrodenfolien
- glänzende und schwarze Oberflächen.
In der Lasertechnik ist die Cap-to-Can-Laserschweißung eine entscheidende Applikation. Dabei gilt es, Pinholes zu detektieren oder bestenfalls ganz zu vermeiden. Unsere Produkte und Optiken haben wir speziell für diese Anwendungen optimiert und innovative Lösungen erarbeitet.
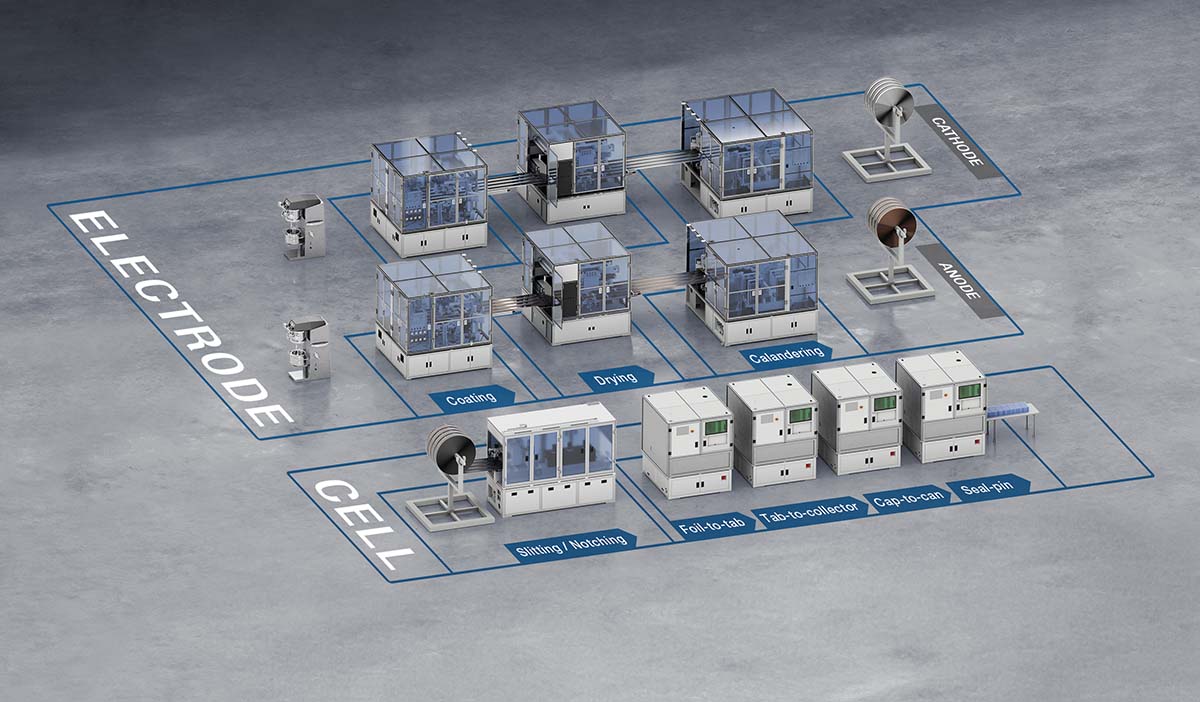
Lösungen für Ihre Fertigungsschritte in der Elektrodenproduktion
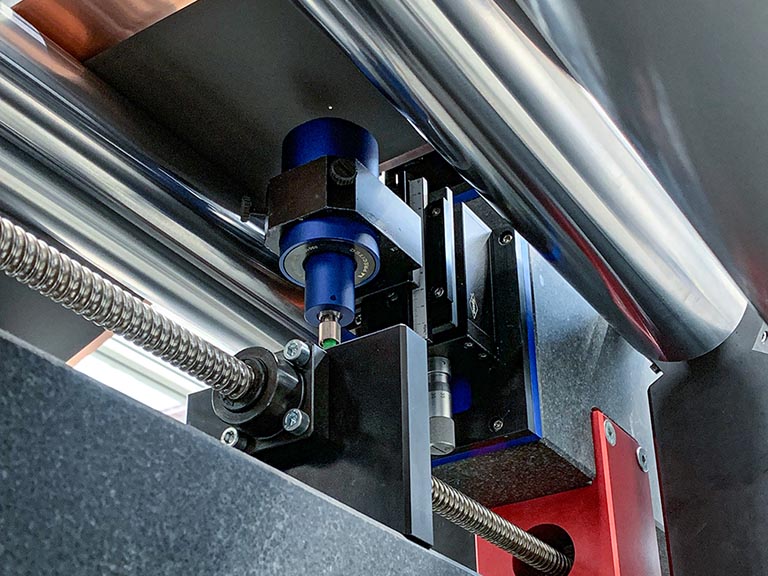
Die exakte Beschichtungsdicke von Elektrodenfolien spielt eine wesentliche Rolle, da sie die Leistung und Lebensdauer der Batterien maßgeblich beeinflussen. Im Produktionsablauf wird die Trägerfolie erst mit dem Slurry kontinuierlich oder intermittierend beschichtet und nachfolgend im Trocknungskanal das Lösungsmittel der Schicht entzogen.
Die Dickenmessungen erfolgen vor und nach dem Trocknungsprozess. Die Beschichtung kann dabei im trockenen oder nassen Zustand sein – d.h. unsere Messung ist immer exakt egal ob die Oberfläche spiegelnd, schwarz oder porös ist. Die Auswirkungen von Vibration und Bandgeschwindigkeit werden dabei kompensiert. Die Welligkeit und Dicke der Folie werden genau analysiert und die Resultate aufgezeigt. Die aktuellen Marktanforderungen sind eine absolute Auflösung von < 1 µm, bei einer Wiederholgenauigkeit von 0,5 µm.
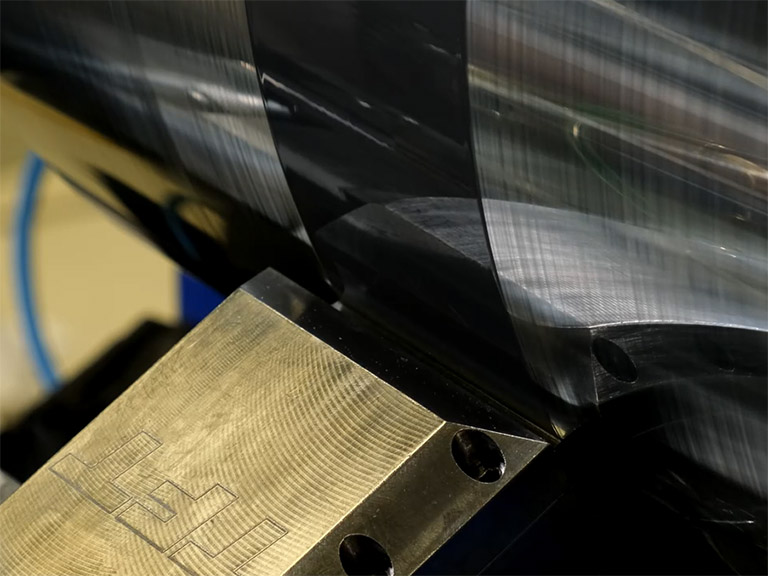
Der exakte Abstand zwischen Schlitzdüse und Trägerfolie ist für die Qualität der Beschichtung und damit der Perfomance der Batteriezelle wesentlich. Die Abstände sind in der Regel zwischen 100 – 300 µm. Ein nicht exakt eingestellter Abstand hat Einfluss auf die Dicke der Beschichtung, die Beschichtungsbreite, sowie die Bilder der unerwünschten Kantenüberhöhung (Edge Superelevation).
Der Realspalt kann beim Einrichten der Maschine exakt vermessen, eingestellt und während des Beschichtens kontinuierlich überwacht werden. In Kombination mit der Vermessung der Beschichtungsdicke, bzw. der Kantenüberhöhung kann ein automatisierter Regelkreis aufgebaut werden, der die Effizienz der Anlage wesentlich erhöht und die Ausbringung steigert.
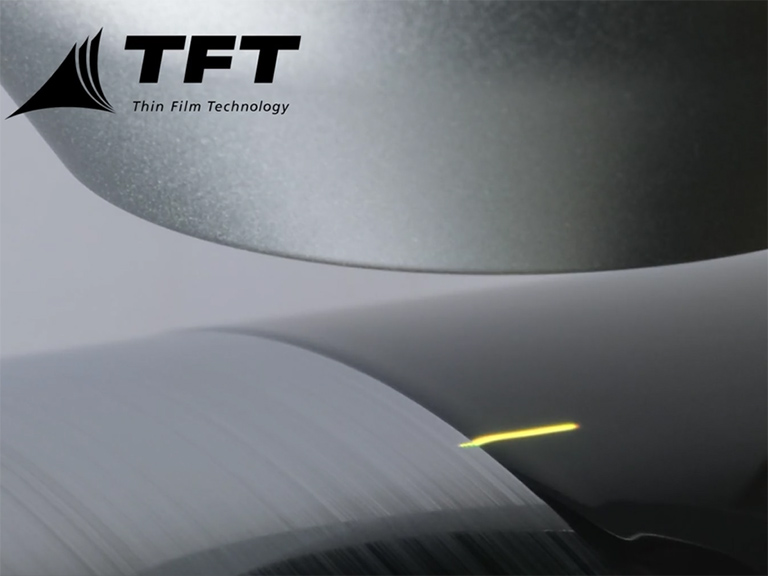
Eine Erhöhung der Kante (Edge Superelevation) entsteht an der Grenze des aufgetragenen Slurrys und kann sich negativ auf die weitere Verarbeitung der Elektrode auswirken, insbesondere beim Aufwickeln. Es kann zu einer asymmetrischen Aufwicklung führen und damit auch zu massiven Handlingsproblemen.
Um die Performance von Batteriezellen zu steigern, versucht man aktuell die Dicke der Beschichtung zu erhöhen. Dickere Beschichtungen neigen aber zudem zur Bildung der Kantenüberhöhung.
Unser Liniensensor ermöglicht eine präzise Vermessung der Kante über eine Länge von bis zu 20 mm während des Fertigungsprozesses. Dabei können sowohl nasse als auch trockene Kanten erfasst werden. Die Vibration des Bandes wird dabei verrechnet. Übergänge von spiegelnden, metallischen Trägerfolien zu schwarzem Slurry können exakt dargestellt werden.
Die Start-/Stopp-Kante tritt beim intermittierenden Beschichten auf. Dabei wird abwechselnd Slurry auf die Trägerfolie aufgetragen bzw. bewusst ausgespart. Die Start-/Stopp-Kanten sind bei dieser Beschichtungsart herausfordernd und müssen überwacht werden, um eine hohe Lebensdauer und Sicherheit der Batteriezelle zu gewährleisten.
Mit unseren Punktsensoren kann der Topographie-Verlauf exakt vermessen und damit mögliche Beschichtungsfehler frühzeitig und exakt erfasst werden.
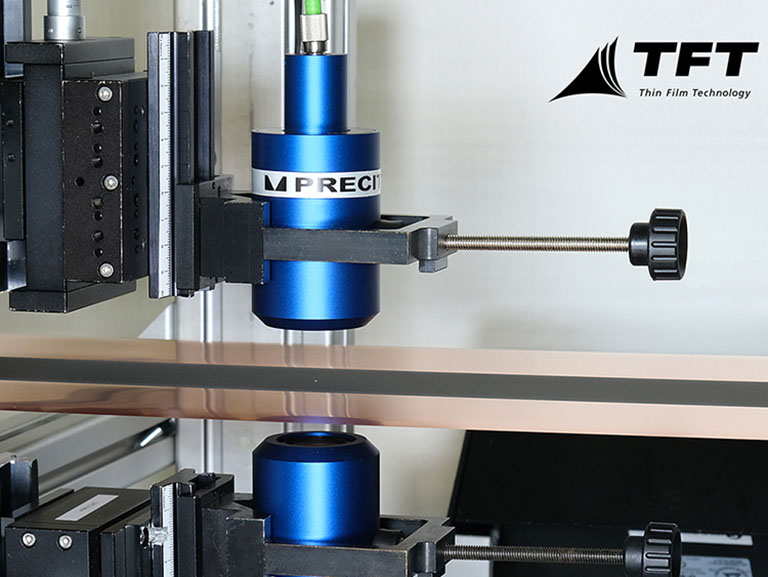
Die exakte Beschichtungsdicke von Elektrodenfolien spielt eine wesentliche Rolle, da sie die Leistung und Lebensdauer der Batterien maßgeblich beeinflussen. Im Produktionsablauf wird die Trägerfolie erst mit dem Slurry kontinuierlich beschichtet und nachfolgend im Trocknungskanal das Lösungsmittel durch Wärmezufuhr der Schicht entzogen. Um eine hohe Anbindekraft des Slurries auf der Trägerfolie zu garantieren, ist die Identifikation der 5 Stadien der Trocknung wesentlich. So muss zum Beispiel die Migration des Binders verhindert werden. Für eine optimierte Trocknung ist zudem der Zeitpunkt der vollständigen Porenentleerung entscheidend.
Unsere Sensoren erlauben diese Zeitpunkte während des Trocknungsprozesses zu erkennen. Damit kann die Trockenlänge verkürzt, die Qualität der Beschichtung optimiert und Energiekosten eingespart werden.
Genaueste Dickenmessungen können auch während des gesamten Trocknungsprozesses erfolgen. Ob nasse oder trockene Schichten, schwarzes oder poröses Grafit oder Kathodenaktivmaterial – das Messergebnis bleibt exakt. Die Auswirkungen von Vibration und Bandgeschwindigkeit werden während der Messung kompensiert.
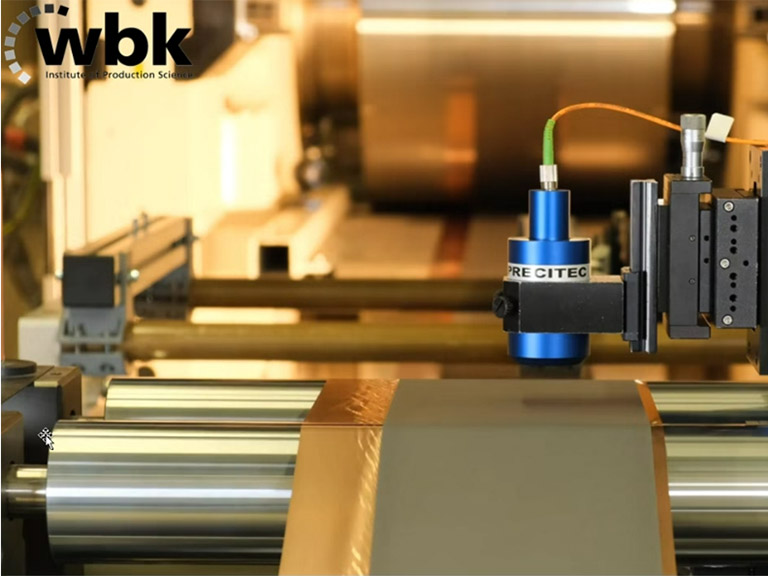
Das Kalandrieren ist der letzte Prozessschritt beim Herstellen der Elektrode. Dabei entscheidet sich wesentlich die finale Dicke und Porosität der Beschichtung. Neben dem Flächengewicht sind dies entscheidende Merkmale für Performance und Sicherheit der Batteriezelle.
Unsere Sensoren erlauben den Kalandrierprozess umfassend zu vermessen. Dabei wird die Dicke der Elektrode vor und nach dem Kalandrieren, der Rundlauf der Kalanderwalzen, sowie die sogenannten Wrinkles vermessen. Das sind Falten am Rand der Beschichtung auf dem Trägermaterial. Vibrationen der Folien werden durch unsere Sensoren kompensiert und Welligkeiten verrechnet. So können zu jeder Zeit exakte Messungen auch bei hohen Bandgeschwindigkeiten von zwischen 100 – 150 m/min realisiert werden.
Beim Kalandrieren werden die Elektrodenfolien komprimiert, also gewalzt. Dieser Prozessschritt entscheidet über die finale Dicke der Elektrodenfolie und damit über die Sicherheit, Lebensdauer und Performance der Batteriezelle.
Für eine optimale Komprimierung der Folien muss der Abstand der beiden Kalanderwalzen exakt eingestellt und während des Komprimierens überwacht werden. Der Abstand der beiden Walzen kann sich durch kleinste Abweichungen des Rundlaufs der Walzen bzw. durch die applizierte Zustellkraft der Walzen ändern. Unsere Sensoren können kleinste Änderungen des Realspalts exakt messen und damit für stets höchste Qualität der Elektroden gewährleisten.
Kalanderwalzen sind massive Stahlwalzen mit Durchmessern größer als 1 m. Die spiegelnden Oberflächen sind exakt geschliffen, um höchste Qualität der gewalzten Elektroden zu ermöglichen. Defekte auf den Walzflächen sowie kleine Abweichungen des Rundlaufs haben direkten Einfluss auf Dicke und Beschaffenheit der Elektrodenfolie. Die Überwachung des Verschleißes der Kalanderwalzen-Oberflächen sowie des Rundlaufs sind daher von größter Bedeutung.
Unsere Sensoren erlauben diese Qualitätsmerkmale zu erfassen. Kleinste Abweichungen vom Rundlauf werden erkannt, kleinste Kratzer auf den Walzflächen werden detektiert.
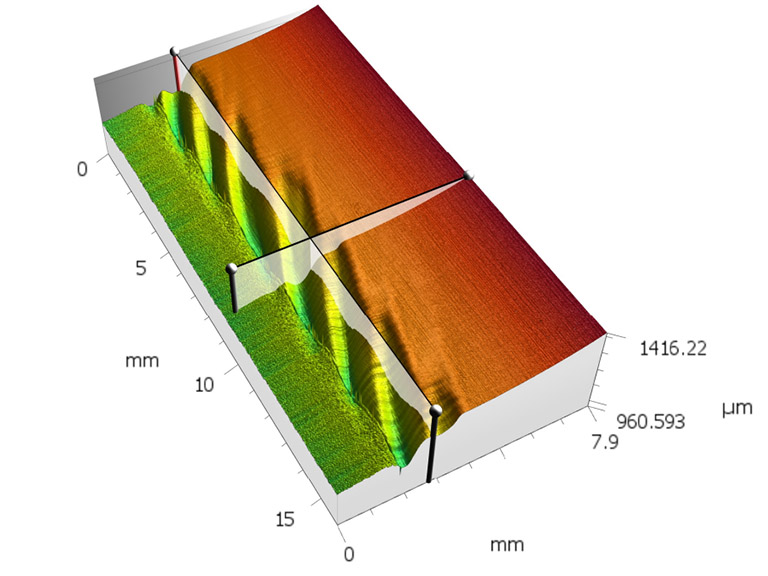
Aufgrund der Walzenkraft und der unterschiedlichen Ausdehnungen vom Beschichtungs- und Trägermaterial kann es nach dem Walzen zur Faltenbildung, den sogenannten Wrinkles kommen. Diese entstehen insbesondere am Rand, also an der Kante von Trägermaterial zu Beschichtung. Falten erschweren die nachfolgenden Fertigungsprozesse signifikant oder machen diese sogar unmöglich.
Mit unserer Sensorik können Wrinkles detektiert und deren Größe vermessen werden. Sind diese zu groß, wird das Material ausgeschleust. Auch ist durch Anpassen der Walzparameter die Bildung von Wrinkles reduzierbar.
Die Separatorfolie trennt die beiden Elektrodenfolien, also die Anode und die Kathode, und verhindert somit Kurzschlüsse. Separatorfolien müssen elektrisch isolierend sein und bestehen daher zumeist aus porösen, mitunter mehrlagigen Kunststoffen wie Polypropylen oder Polyethylen. Diese Folien haben Dicken zwischen 15 und 25 µm und dürfen nicht durch Fremdpartikel beschädigt sein. Wird die Separatorfolie durchstoßen gibt es einen Kurzschluss und die Gefahr einer Brandentzündung ist groß. (thermal runaway).
Mit unseren Sensoren können wir die Dicke und Integrität von Separatorfolien vermessen und auch die Dicke der Einzelschichten auflösen.
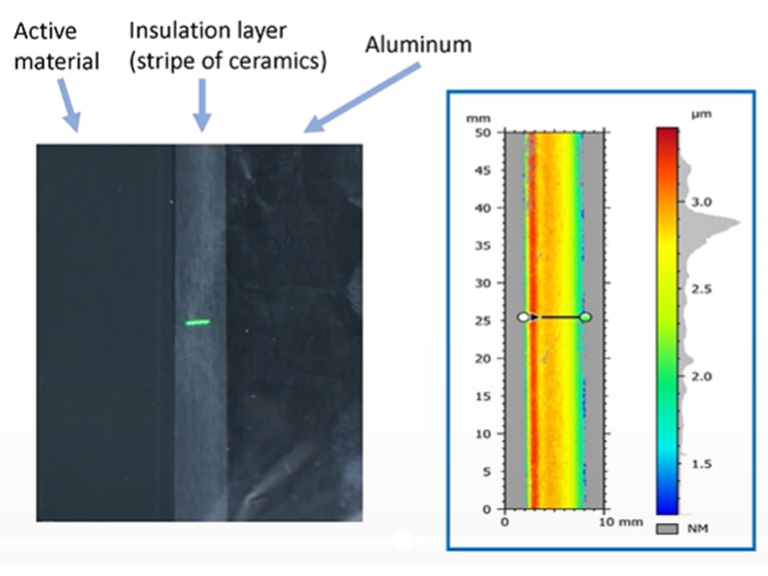
Zur Verbesserung der Sicherheit von Batteriezellen wird mitunter ein sogenannter Insulation Layer auf die Elektrode appliziert. Dieser besteht aus einem Keramikstreifen, der neben das Aktivmaterial aufgetragen wird.
Hintergrund ist, dass sich Separatoren aus Polypropylen ab Temperaturen von 110°C zusammenziehen und ab 150°C sogar schmelzen. Der Streifen aus Keramik verhindert die mögliche Gefahr eines Kurzschlusses zwischen Kathode und Anode und erhöht damit die Sicherheit der Zelle.
Marktübliche Dicken des Insulation Layers betragen zwischen 3 – 10 µm. Für beste Qualitäten und eine effiziente Produktion werden diese bei Rolle-zu-Rolle-Prozessen - auch bei hohen Bandgeschwindigkeiten von bis zu 150 m/min - inline vermessen. Dabei können zum Beispiel das Dickenprofil von Aluminiumoxid (Al2O3) dargestellt und Defekte erkannt werden. Ein möglicher Spalt zwischen Aktivmaterial und Keramikstreifen wird detektiert und auch ein Überlapp von Keramik über Aktivmaterial lässt sich darstellen.
Lösungen für Ihre Fertigungsschritte in der Zellproduktion
Mit Hilfe des Laserschneidens werden Elektrodenfolien auf die finale Geometrie gebracht. Diese besteht dabei aus Schnitten mit Ableiterfahnen; bei zylindrischen 4680 Zellen aber auch nur aus geraden Schnitten. Beim Laserschneiden sollen die Wärmeeinflusszone aber auch der Schnittgrat möglichst gering sein. Durch intelligente Schneidoptiken lassen sich Position und Fokuslage exakt einstellen und damit höchste Schnittqualität garantieren. Des Weiteren werden mit Kameras und Photodioden-Sensoren die Qualität der Schnitte ausgewertet und getrackt.
In der Batteriefertigung werden beschichtete Kupfer- und Aluminiumfolien getrennt und später zu kompletten Zellen aufgebaut. Für die Bearbeitung der dünnen Schichten zwischen 100 und 250 µm kann der Laser seine Stärken voll ausspielen. Mechanisch trennende Verfahren führen oft zu Beschädigungen der Oberflächenbeschichtung – beim Laser wird das Werkstück berührungslos im Coil-to-Coil-Verfahren bearbeitet. Durch die Verwendung von Prozessgasen werden mögliche Partikel nach unten hin abgeführt, wodurch die Materialoberfläche nicht verunreinigt wird. Eine dynamische und präzise Abstandsregelung sorgt für eine hohe Qualität der Schnittkanten und geringe Grathöhen.
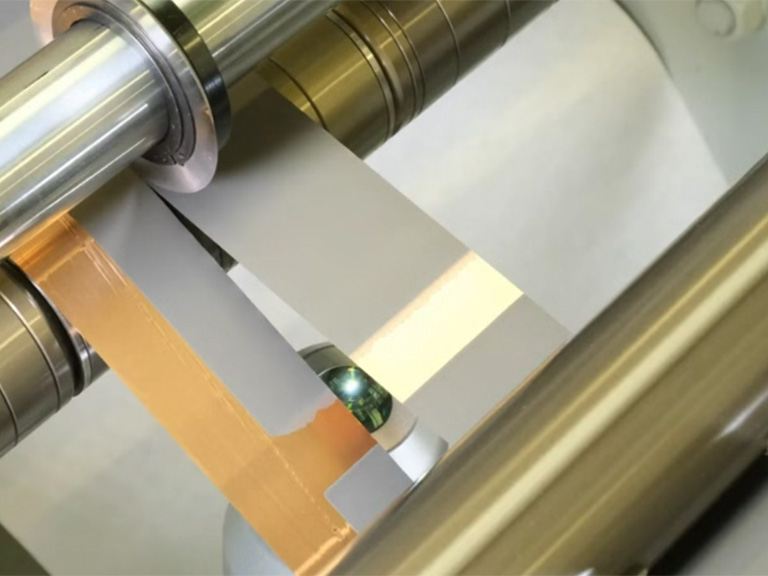
Wird der Separator durchstoßen, kommt es zum Kurzschluss und die Gefahr einer Brandentzündung ist groß (thermal runaway). Separatoren haben in der Regel eine Dicke von ca. 20 µm. Daher ist es von größter Bedeutung, Schnittgrate von ca.10 µm zu detektieren.
Die Vermessung der Grate kann dabei sowohl die Geometrie und Form der Metallfolien darstellen als auch die Topographie der Beschichtung inkl. der darunterliegenden Metallfolie. Dabei kommen verschiedenen Techniken zum Einsatz, die die Grate entweder von unten oder von der Seite vermessen, je nach Aufgabe und Anforderung. Integriert in ein Rolle-zu-Rolle-System detektieren wir daher zuverlässig Grate und geben dadurch Hinweise auf die Qualität der Rollschneider (Predictive Maintanance) bzw. des Laserschnitts.
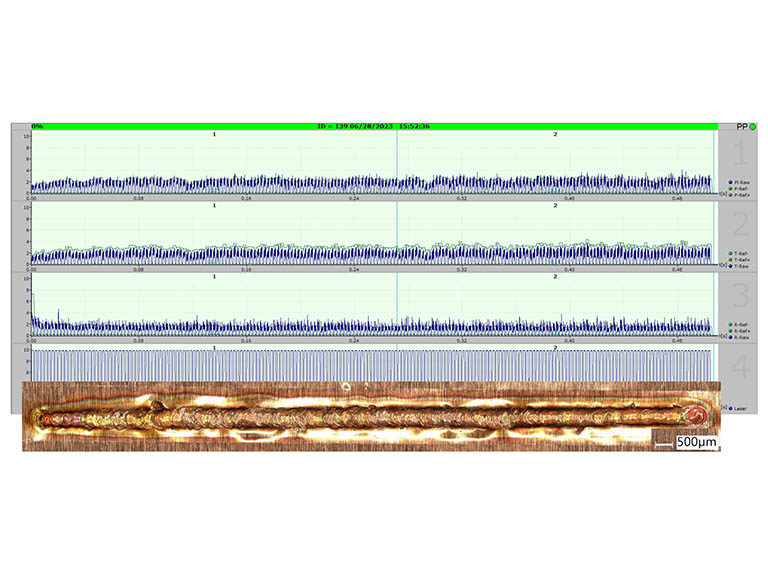
Batterien bestehen aus mehreren Schichten dünner Kupferfolien und Aluminiumfolien (5 – 10 µm), die miteinander verschweißt werden müssen, um eine stabile und leistungsfähige Batterie zu erzeugen. Dabei werden üblicherweise 60 - 100 Folien verschweißt. Je nach gewünschter Kapazität und Leistungsfähigkeit der Batterie werden dann mehrere dieser Schichten übereinandergestapelt.
Beim Verschweißen des Folienstapels ist neben einer exakten Einspannung des Folienstapels auch eine intelligente Schweißstrategie wichtig. Diese erlaubt es, mit wenig Verzug und ohne Durchbrand eine sichere Verbindung von der ersten bis zur letzten Folie zu realisieren. Durch die Verwendung von Prozessüberwachungssystemen können hierbei Schweißanomalien und kleinste Abweichungen detektiert werden, um die Qualität und Zuverlässigkeit der Schweißnaht sicherzustellen. Schlussendlich führt dies zu einer höheren Produktionsleistung und einer besseren Produktqualität.
Beim Cap-to-Can Laserschweißen wird ein Metalldeckel (Cap) auf einen Metallbehälter (Can) aufgeschweißt. Diese Art des Laserschweißens wird oft in der Batterieproduktion eingesetzt, um die Elektrolyte von der Außenwelt zu isolieren und die Leckage von Flüssigkeiten zu verhindern. Materialien sind hier Aluminium oder vernickelter Stahl.
Die Cap-to-Can Laserschweißung wird bei zylindrischen aber auch bei prismatischen Batteriezellen eingesetzt. In beiden Fällen ist die Qualität der Schweißnaht von entscheidender Bedeutung für die Leistung und Zuverlässigkeit der Batterie.
Bei großen Batteriezellen, wie den 4680, ist die Rundheit der Can nicht immer 100%ig gegeben. Es ist jedoch für die Dichtheit der Schweißnaht wesentlich, dass der Laserstrahl entlang der Kontur der Can geführt wird. Die reale Kontur kann exakt und schnell mit dem ScanMaster vermessen und der Laserstrahl entsprechend angepasst werden. Damit erreicht man qualitativ hochwertige Schweißnähte, ohne in die Zelle einzuschweißen.
Ein typischer Defekt beim Cap-to-Can Laserschweißen ist das sogenannte Pinhole, das zur Undichtheit der Schweißverbindung führen kann. Große Pinholes können als Schweißanomalie mit dem Laser Welding Monitor detektiert werden. Kleinste Defekte auf der Schweißnaht werden im Post-Prozess durch Vermessung der Topographie der Schweißnaht erkannt. Eine Nacharbeitung der Zelle ist dann möglich, wodurch Ausschuss reduziert wird.
Während der Montage der Batteriezelle wird der Elektrolyt gleichmäßig und vollständig in die Zelle eingefüllt und verteilt, um eine optimale Leistung zu gewährleisten. Rückstände des Elektrolyten auf der Außenseite der Batteriezellen beeinträchtigen die Produktsicherheit. Je mehr Batterien produziert werden, desto dringender besteht der Bedarf für das automatisierte Erkennen und Ausschleusen von verunreinigten Stellen an der Einfüllseite der Batteriezelle in der Produktionslinie. Im Folgeprozess, der sogenannten Seal Pin Schweißung, wird die Einfüllöffnung zylindrischer oder prismatischer Zellen per Laser dichtgeschweißt. Rückstände des Elektrolyts beeinflussen die Qualität der Schweißnaht und können zu Leckagestellen oder erheblichen Verunreinigungen durch Schweißspritzer führen. Die Zelle wäre damit undicht und somit Ausschuss.
Nach dem Befüllen der Batteriezelle mit dem Elektrolyt wird die Einfüllöffnung mit einem Deckel verschlossen und mit Laserlicht dichtgeschweißt. Damit wird die Zelle versiegelt und das Austreten des Elektrolyten verhindert. Die Zelle ist damit dicht.
Die Verschweißung von Batteriezellen ist ein kritischer Prozessschritt, da es sich hierbei um eine Dichtheitsschweißung handelt. Ist die Zelle undicht, ist sie Ausschuss. Verunreinigungen oder Spritzer könnten zu kleinsten Leckagestellen in der Schweißnaht führen. Eine präzise und punktgenaue Schweißung des Seal Pins ist daher von großer Bedeutung, um sicherzustellen, dass die Zelle versiegelt bleibt und kein Elektrolyt austreten kann. Ziel sind verzugsfreie und dichte Nähte mit geringem und lokal begrenztem Wärmeeintrag. Jede einzelne Schweißung kann online überwacht, bewertet und dokumentiert werden. Unsere Systeme erkennen Unregelmäßigkeiten und fehlerhafte Schweißungen. Eine 100%ige Rückverfolgbarkeit und Transparenz Ihrer Prozesse ist sichergestellt.
Unterschiedliche Zelltypen für verschiedene Applikationen
In der e-Mobility werden in der Regel drei Typen von Lithium-Ionen-Batterien verwendet. Die Batterien arbeiten nach dem gleichen Funktionsprinzip und besitzen eine hohe Energiedichte, um eine hohe Reichweite gewährleisten zu können. Im Einsatz sind Pouchzellen, prismatische Zellen und zylindrische Zellen, die dann zu Batteriemodulen verbunden werden, um die notwendige Leistung bereitstellen zu können. Aber wie unterscheiden sich diese Zelltypen?
Weitere Anwendungsfelder in der e-Mobility
Brennstoffzelle
Eine Brennstoffzelle besteht aus zahlreichen Bipolarplatten, die gasdicht verschweißt werden müssen. Meistens sind dabei die Schweißgeschwindigkeiten sehr hoch - ähnlich wie der Qualitätsanspruch an die Schweißnaht. Des Weiteren müssen für eine hohe Performance der Brennstoffzellen geometrische Kenngrößen der Bipolarplatten exakt eingehalten werden. Diese vermessen wir mit unseren Sensoren der 3D-Messtechnik.
Antriebsstrang
Der elektrische Antriebsstrang besteht u.a. aus Stator, Rotor und der Leistungselektronik. Für hochwertige Laserschweißungen bei Statoren (Hairpin-Schweißungen) sind gut abisolierte Hairpin-Drähte entscheidend. Wir können sowohl Lackrückstände an Drähten detektieren als auch adaptive Laserschweißprozesse ermöglichen.