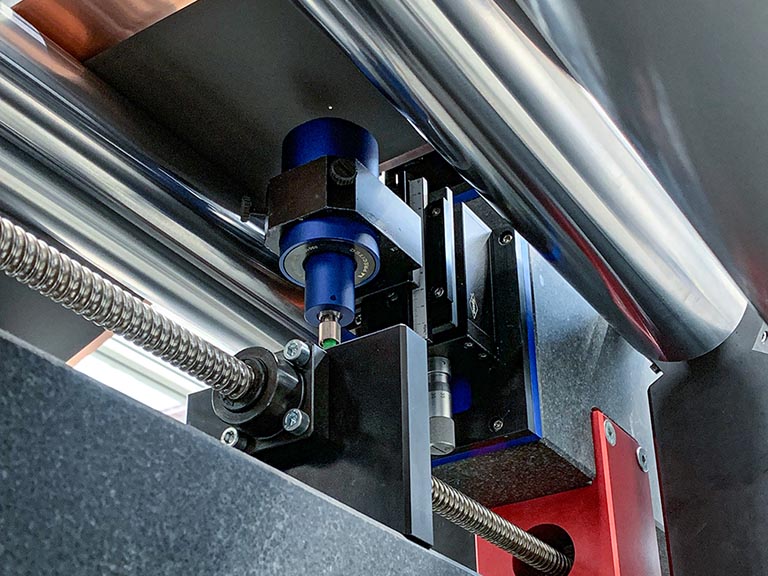
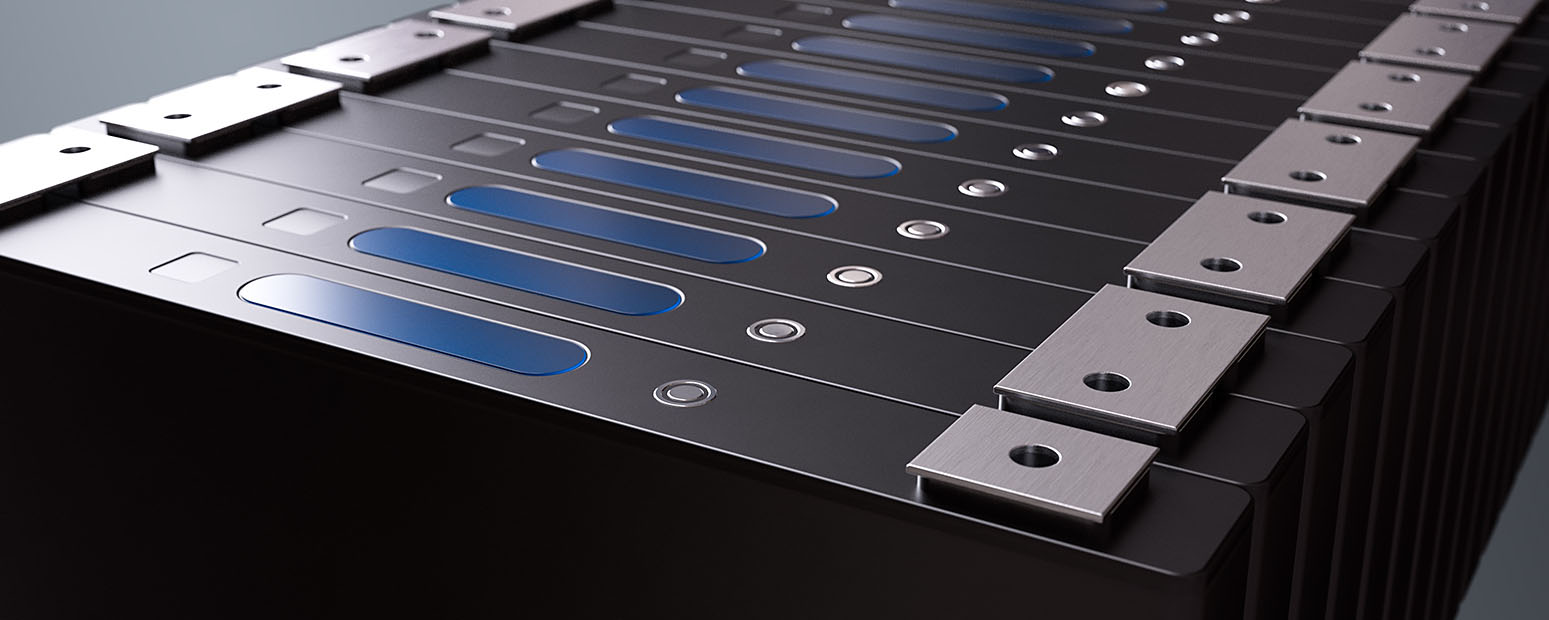
Soluzioni efficienti per la produzione di celle per batterie agli ioni di litio
Nella produzione di elettrodi, le celle delle batterie sono costituite da strati alternati di lamine anodiche e catodiche. Questi sono separati dal cosiddetto separatore. La pila di fogli viene poi arrotolata, imballata in un alloggiamento metallico e le batterie vengono saldate in modo sicuro.
I nostri sistemi di controllo della qualità sono utilizzati in numerose fasi del processo per garantire una produzione efficiente delle celle della batteria. Ciò include, ad esempio, la misurazione dello spessore della lamina dell'elettrodo, il controllo della bava di taglio e la saldatura laser degli strati di lamina (da lamina a lamina) e dell'alloggiamento con il coperchio (da tappo a lattina).
Il requisito fondamentale per il cliente è la precisione: < 1 micrometro. I nostri sensori soddisfano questo requisito e sono ottimizzati per gli ambienti di produzione delle celle per batterie, le cosiddette applicazioni roll-to-roll:
alte velocità del nastro
lamine di elettrodi vibranti
superfici lucide e nere
Nella tecnologia laser, la saldatura laser cap-to-can è un'applicazione cruciale. L'obiettivo è individuare i fori di spillo o, nel migliore dei casi, evitarli del tutto. Abbiamo ottimizzato i nostri prodotti e le nostre ottiche specificamente per queste applicazioni e abbiamo sviluppato soluzioni innovative.
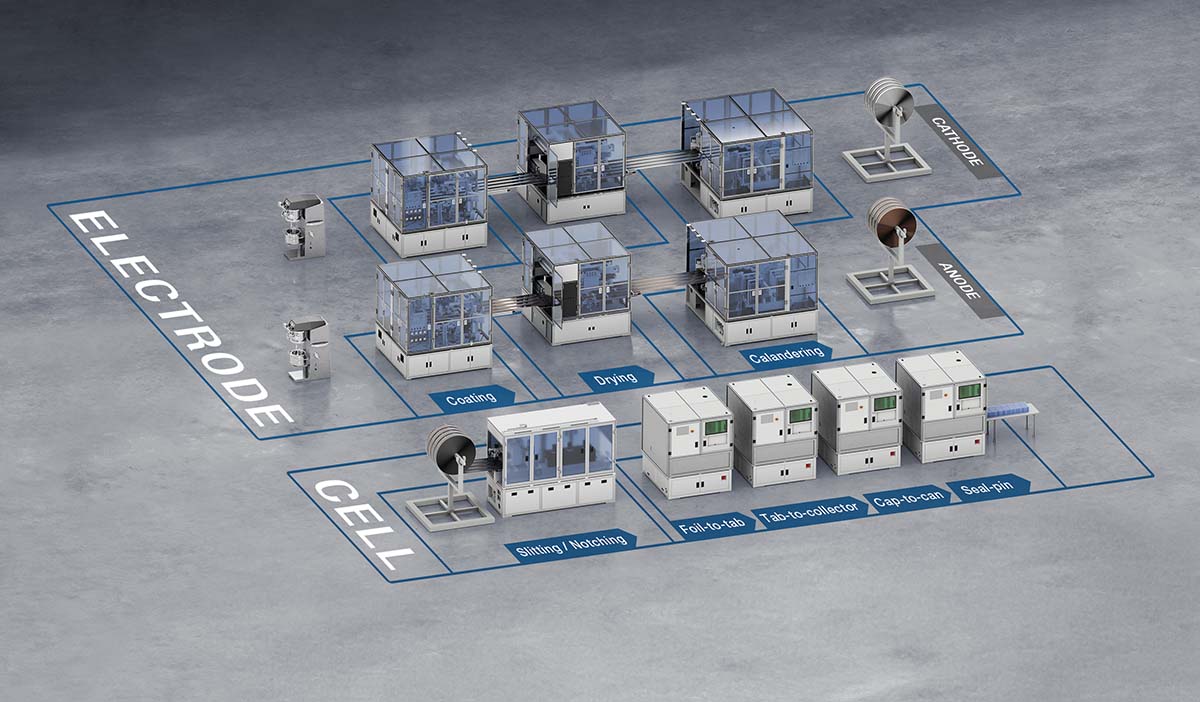
Soluzioni per le vostre fasi di lavorazione nella produzione di elettrodi
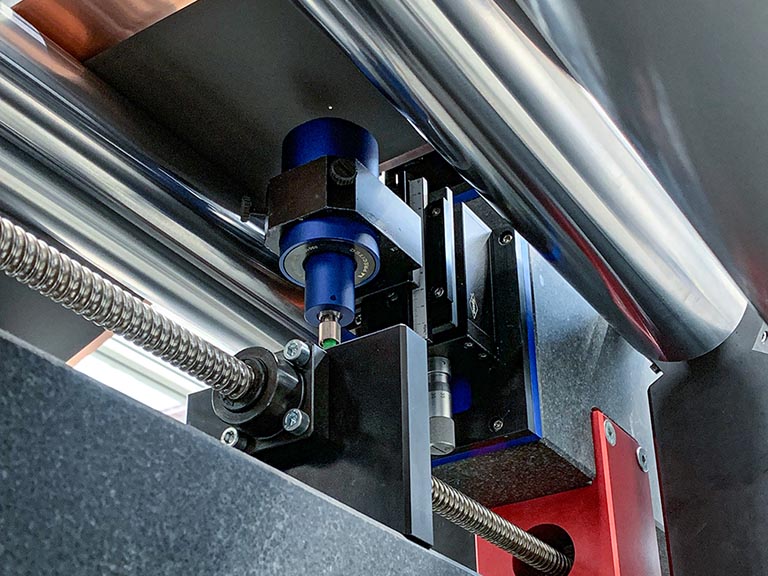
L'esatto valore dello spessore del rivestimento delle lamine degli elettrodi ha un ruolo fondamentale nella produzione della batterie, in quanto, influisce in modo significativo sulle prestazioni e sulla durata delle stesse. Nel processo di produzione, il film di supporto viene rivestito con un impasto in modo continuo o intermittente, quindi il solvente viene rimosso dallo strato nel tunnel di essiccazione.
La misura dello spessore viene effettuata prima e dopo il processo di essiccazione. Il rivestimento può essere quindi asciutto o bagnato, ma la nostra misura è sempre esatta, indipendentemente dal fatto che la superficie sia riflettente, nera o porosa. Anche gli effetti delle vibrazioni e della velocità del nastro vengono compensati. L'ondulazione e lo spessore del film sono analizzati con precisione e ne vengono visualizzati i risultati. I requisiti attuali del mercato sono: precisione assoluta < 1 µm, con ripetibilità di ± 0,5 µm.
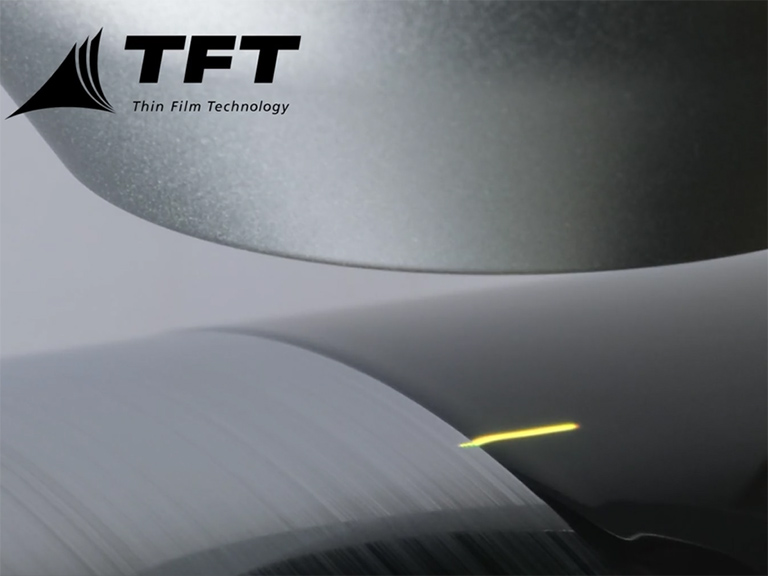
La sopraelevazione del bordo si verifica al limite esterno dell'impasto di rivestimento quando viene applicato; e può avere un effetto negativo sulla successiva lavorazione dell'elettrodo, soprattutto durante la fase di avvolgimento. Può, infatti, portare ad un avvolgimento asimmetrico e quindi ad importanti problemi di movimentazione.
Per aumentare le prestazioni delle celle delle batterie, attualmente si cerca di aumentare lo spessore del rivestimento. Tuttavia, anche i rivestimenti più spessi non sono immuni dal formare una sopraelevazione del bordo.
Il nostro sensore a linea consente di misurare con precisione lo spessore del bordo durante il processo di produzione, grazie a linee di misura lunghe fino a 20 mm. È possibile rilevare sia i bordi bagnati che quelli asciutti. Si tiene conto delle vibrazioni del nastro. È possibile visualizzare con precisione le transizioni da lamina metallica riflettente a rivestimento nero.
Il bordo di inizio/fine rivestimento si presenta durante il processo di ricopertura intermittente. In questo processo, l'impasto viene applicato alternativamente alla lamina portante o deliberatamente tralasciato. I bordi di avvio/arresto rappresentano una sfida per questo tipo di rivestimento e devono essere monitorati per garantire durabilità e sicurezza della cella della batteria.
Con i nostri sensori a punto, è possibile misurare con precisione il profilo topografico e quindi individuare subito ed accuratamente eventuali difetti del rivestimento.
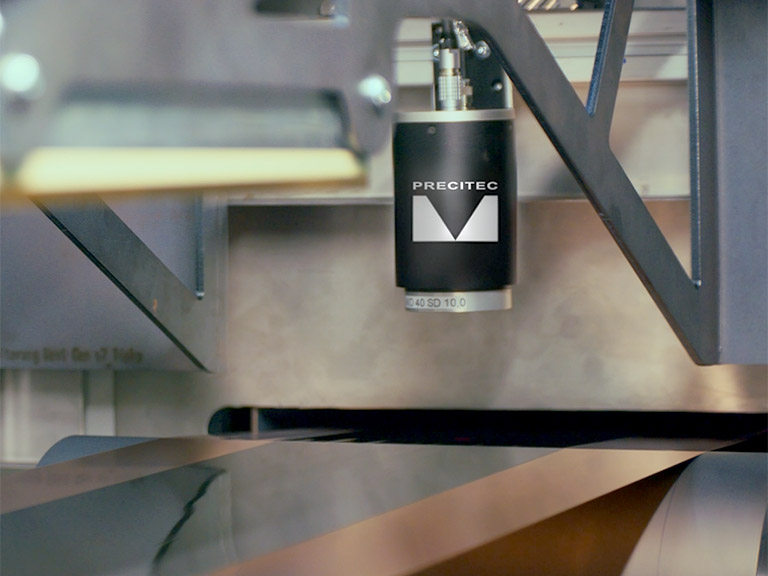
L'essiccazione dei fogli rivestiti per batterie rappresenta una fase fondamentale nella produzione degli elettrodi. A causa del suo elevato fabbisogno energetico, questa fase offre un notevole potenziale di riduzione dei costi e dell'impronta di CO₂, indipendentemente dal fatto che l'essiccazione avvenga per convezione, con laser, con radiatori a infrarossi o con processi ibridi.
Oltre agli aspetti energetici, il processo di essiccazione ha anche un'influenza decisiva sulla qualità degli elettrodi. Particolarmente critica è la fase che inizia con lo svuotamento dei pori: se in questa fase l'essiccazione è troppo intensa, le forze capillari possono attirare il legante sulla superficie dello slurry. La conseguenza è una migrazione del legante che impedisce al materiale attivo di rimanere saldamente legato al conduttore, con un rischio per le prestazioni e la durata della batteria.
La nostra tecnologia dei sensori consente di identificare chiaramente le cinque fasi caratteristiche del processo di essiccazione. Grazie all'integrazione in linea nei processi roll-to-roll, è possibile determinare con precisione lo stato attuale di essiccazione e controllare il processo in modo mirato. Ciò comporta una significativa riduzione dei costi energetici, un miglioramento sostenibile della qualità del prodotto e una maggiore sicurezza complessiva del processo.
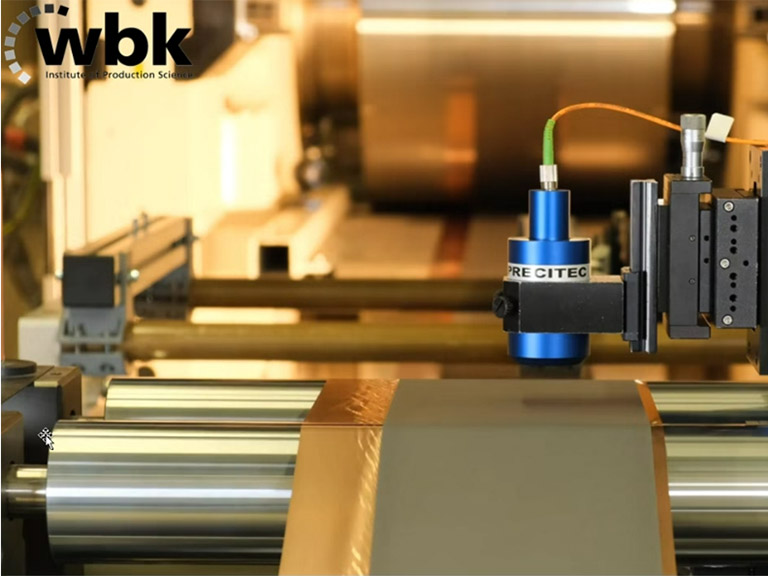
La calandratura è l'ultima fase del processo di produzione dell'elettrodo. È qui che si determinano essenzialmente lo spessore finale e la porosità del rivestimento; oltre al peso per unità di superficie, queste sono caratteristiche decisive per le prestazioni e la sicurezza della cella della batteria.
I nostri sensori consentono una misura completa del processo di calandratura. Vengono misurati lo spessore dell'elettrodo prima e dopo la calandratura, la concentricità dei rulli della calandra e le cosiddette grinze. Si tratta di grinze sul bordo del rivestimento del substrato. Le vibrazioni dei fogli vengono compensate dai nostri sensori e viene calcolata l'ondulazione. Ciò significa che è possibile effettuare misure precise in qualsiasi momento, anche a velocità elevate del nastro: tra 100 e 150 m/min.
I rulli di laminazione sono rulli in acciaio massiccio con diametro superiore a 1m. Le superfici a specchio sono rettificate con precisione per garantire la massima qualità degli elettrodi laminati. I difetti sulle superfici di laminazione e le piccole deviazioni della concentricità hanno un'influenza diretta sullo spessore e sulle condizioni della lamina dell'elettrodo. Il monitoraggio dell'usura delle superfici dei rulli di calandratura e della concentricità è quindi di estrema importanza.
I nostri sensori consentono di registrare queste caratteristiche di qualità: vengono rilevate le più piccole deviazioni dalla concentricità e i più piccoli graffi sulle superfici dei rulli.
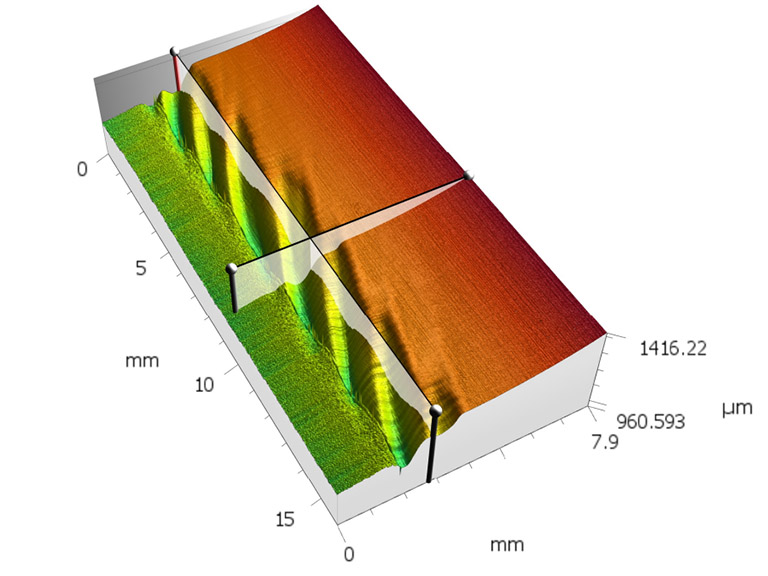
A causa della forza di laminazione e delle diverse espansioni del materiale del rivestimento e della lamina, dopo la laminazione possono formarsi delle grinze. Queste si formano soprattutto sul bordo della lamina conduttrice e del rivestimento. Le grinze complicano notevolmente i processi produttivi successivi o addirittura li rendono impossibili.
Con i nostri sensori è possibile rilevare le grinze e misurarne le dimensioni: se sono troppo grandi, il materiale viene scartato. La formazione di grinze può essere ridotta anche regolando i parametri di laminazione.
Il foglio separatore divide le due lamine elettrodiche, cioè l'anodo e il catodo, evitando così i cortocircuiti. I fogli separatori devono essere elettricamente isolanti e pertanto sono solitamente costituiti da materiali plastico poroso, talvolta multistrato, come il polipropilene o il polietilene. Questi film, hanno spessori compresi tra 15 e 25µm e non devono essere danneggiati da particelle estranee. Se la pellicola di separazione viene penetrata, si verifica un cortocircuito e il rischio di incendio è elevato (fuga termica).
Con i nostri sensori possiamo misurare lo spessore e l'integrità dei fogli separatori e misurare lo spessore dei singoli strati.
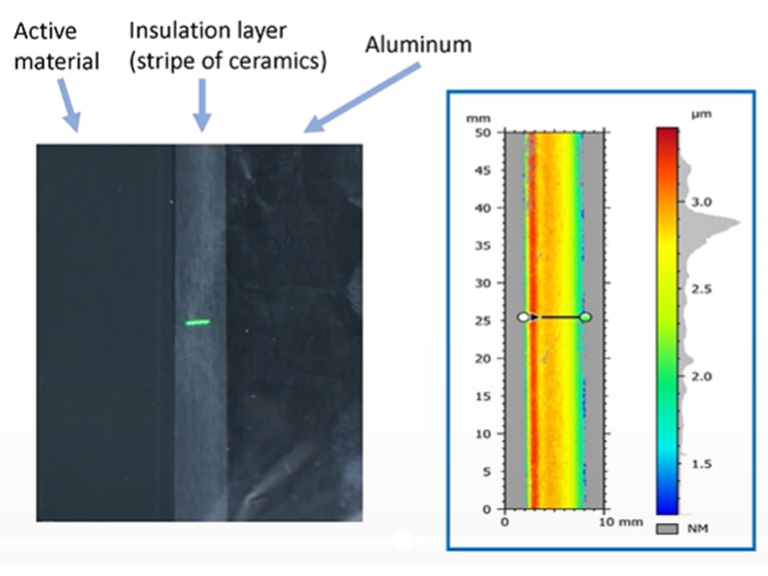
Per migliorare la sicurezza delle celle delle batterie, a volte viene applicato uno strato isolante all'elettrodo. Si tratta di una striscia di ceramica che viene applicata accanto al materiale attivo.
Il motivo è che i separatori in polipropilene si contraggono a temperature di 110°C e addirittura si fondono a 150°C e oltre. La striscia di ceramica previene il rischio potenziale di un cortocircuito tra il catodo e l'anodo, aumentando così la sicurezza della cella.
Gli spessori standard di mercato dello strato isolante sono compresi tra 3 e 10 µm. Per ottenere la migliore qualità e una produzione efficiente, questi spessori vengono misurati in linea nei processi roll-to-roll, anche a velocità elevate del nastro, fino a 150 m/min. Ad esempio, è possibile visualizzare il profilo di spessore dell'ossido di alluminio (Al2O3) e rilevare i difetti. È possibile rilevare un eventuale divario tra il materiale attivo e la striscia di ceramica e visualizzare la sovrapposizione della ceramica sul materiale attivo.
Soluzioni per le vostre fasi di produzione nella produzione cellulare
Per il taglio diritto della lamina dell’elettrodo, Precitec ha sviluppato la cosiddetta soluzione di “taglio laser assistito da gas su rullo scanalato”. Questo metodo innovativo garantisce una qualità di taglio costantemente elevata, guidando con precisione la lamina durante il processo e riducendo al minimo le vibrazioni. Il taglio diretto sul rullo consente di ridurre la dimensione del punto laser e la potenza media del laser, minimizzando significativamente la zona termicamente alterata (HAZ) e migliorando la qualità complessiva del taglio.
Il taglio laser assistito da gas offre inoltre un processo più pulito ed efficiente. Le particelle e i residui generati durante il taglio vengono convogliati all'interno del rullo scanalato e rimossi in modo sicuro tramite un sistema di aspirazione integrato – evitando così la contaminazione dell’impianto di taglio laser.
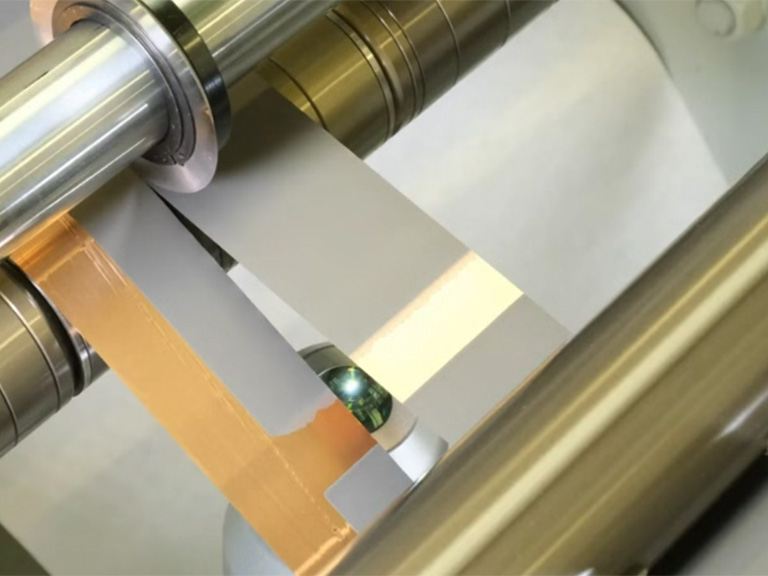
Se il separatore viene penetrato, si verifica un cortocircuito e il rischio di incendio è elevato (fuga termica). I separatori hanno solitamente uno spessore di circa 20 µm. Pertanto, è estremamente importante rilevare le bave di taglio di dimensioni di circa 10 µm.
La misura delle bave può mostrare la geometria e la forma delle lamine metalliche, nonché la topografia del rivestimento, compresa la lamina metallica sottostante. Per misurare le bave si utilizzano tecniche diverse, dal basso o dal lato, a seconda dell'obiettivo e dei requisiti. I nostri sensori, Integrati in un sistema roll-to-roll, rilevano in modo affidabile le bave e forniscono, quindi, informazioni sulla qualità della taglierina (manutenzione predittiva) o del taglio laser.
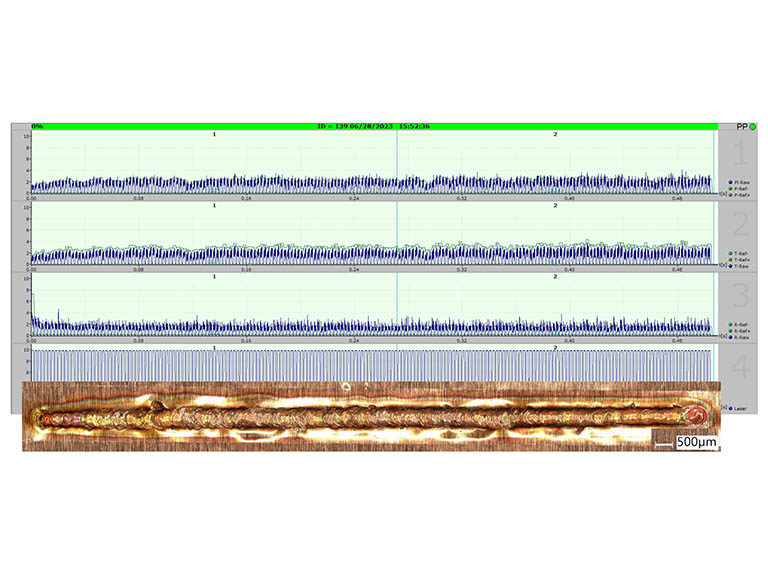
Le celle delle batterie sono costituite da diversi strati di sottili lamine di rame ed alluminio (5-10 µm) che devono essere saldati insieme per creare una batteria stabile e potente. Di solito vengono saldate insieme 60-100 lamine. A seconda della capacità e delle prestazioni desiderate della batteria, diversi di questi strati vengono poi impilati l'uno sull'altro.
Durante la saldatura della pila di lamine, è importante una strategia di saldatura intelligente, oltre ad un serraggio preciso della pila stessa. In questo modo è possibile realizzare una connessione sicura dal primo all'ultimo film, con una minima distorsione e senza bruciature. Utilizzando sistemi di monitoraggio del processo laser, è possibile rilevare le anomalie di saldatura e le più piccole deviazioni, per garantire la qualità e l'affidabilità del cordone di saldatura. In definitiva, questo porta a una maggiore produzione e a una migliore qualità del prodotto.
La saldatura laser coperchio/conteitore consiste nel saldare un coperchio metallico (cap) su un contenitore metallico (can). Questo tipo di saldatura laser è spesso utilizzato nella produzione di batterie per isolare gli elettroliti dal mondo esterno e per evitare perdite di liquidi. I materiali sono alluminio o acciaio nichelato.
La saldatura laser cap-to-can viene utilizzata per celle di batterie cilindriche ma anche prismatiche. In entrambi i casi, la qualità della saldatura è fondamentale per le prestazioni e l'affidabilità della batteria.
Con le celle di grandi dimensioni, come la 4680, la forma cilindrica del contenitore non è sempre al 100%. Tuttavia, per la tenuta della saldatura è essenziale che il raggio laser sia guidato lungo il contorno del contenitore. Il contorno reale può essere misurato esattamente e rapidamente con lo ScanMaster e il raggio laser può essere regolato di conseguenza. In questo modo è possibile ottenere cordoni di saldatura di alta qualità senza saldare nella cella.
Un difetto tipico della saldatura laser cap-to-can è il cosiddetto pinhole (forellino), che può portare alla mancata tenuta del giunto saldato. I pinhole di grandi dimensioni possono essere rilevati come anomalie di saldatura con il Laser Welding Monitor. I difetti più piccoli sul cordone di saldatura vengono rilevati nel post-processo misurando la topografia del cordone di saldatura. È quindi possibile rilavorare la cella, riducendone gli scarti.
Durante l'assemblaggio della cella della batteria, l'elettrolita viene riempito e distribuito in modo uniforme e completo nella cella per garantire prestazioni ottimali. I residui di elettrolita all'esterno delle celle compromettono la sicurezza del prodotto. Più le batterie vengono prodotte, più è stringente la necessità di rilevare ed eliminare automaticamente le aree contaminate sul lato del riempimento della cella nella linea di produzione. Nel processo successivo, noto come saldatura dei perni di tenuta, l'apertura per il riempimento delle celle cilindriche o prismatiche viene siggilata mediante saldatura laser. I residui di elettrolita influenzano la qualità del cordone di saldatura e possono causare perdite o una notevole contaminazione aumentando notevolmente gli spruzzi di saldatura. In tal caso, la cella risulterebbe permeabile e quindi da scartare.
Dopo aver riempito la cella della batteria con l'elettrolita, il foro di riempimento viene chiuso con un coperchio e saldato a tenuta mediante laser: questa operazione sigilla la cella ed impedisce all'elettrolita di fuoriuscire. La cella è quindi sigillata.
La saldatura delle celle della batteria è una fase critica del processo, in quanto si tratta di una saldatura a tenuta. Se la cella perde, è da rottamare. Impurità o schizzi potrebbero causare piccole perdite nella tenuta della saldatura. Una saldatura precisa e a punti del perno di tenuta è quindi di grande importanza per garantire che la cella rimanga sigillata e che l'elettrolita non possa fuoriuscire. L'obiettivo è quello di ottenere saldature prive di distorsioni e ben salde, con un apporto di calore basso e localmente limitato. Ogni singola saldatura può essere monitorata, valutata e documentata online. I nostri sistemi rilevano le irregolarità e le saldature difettose. La tracciabilità e la trasparenza dei processi sono garantite al 100%.
Ulteriori campi di applicazione della mobilità elettrica
Nella mobilità elettrica vengono generalmente utilizzati tre tipi di batterie agli ioni di litio. Le batterie funzionano secondo lo stesso principio funzionale e hanno un'elevata densità energetica per garantire una lunga autonomia. Vengono utilizzate celle a sacchetto (pouch cells) , celle cilindriche e celle prismatiche, che vengono poi collegate per formare moduli di batterie in grado di fornire la potenza necessaria. Ma, come si differenziano questi tipi di celle?
Ulteriori campi di applicazione della mobilità elettrica
Celle a combustibile
Una cella a combustibile è costituita da numerose piastre bipolari che devono essere saldate a tenuta di gas. Nella maggior parte dei casi, le velocità di saldatura sono molto elevate, così come i requisiti di qualità del cordone di saldatura. Inoltre, i parametri geometrici delle piastre bipolari devono essere mantenuti con precisione per garantire elevate prestazioni della cella a combustibile: noi li misuriamo con i nostri sensori di misura 3D.
Propulsione
I moduli dell'azionamento elettrico sono costituiti , tra l'altro, dallo statore, dal rotore e dall'elettronica di potenza. Per una saldatura laser di elevata qualità degli statori (saldatura degli hairpin), sono fondamentali hairpin ben "spellati" (rimozione del rivestimento). Siamo in grado di rilevare i residui di vernice sui fili e di adattarne i processi di saldatura laser di conseguenza.